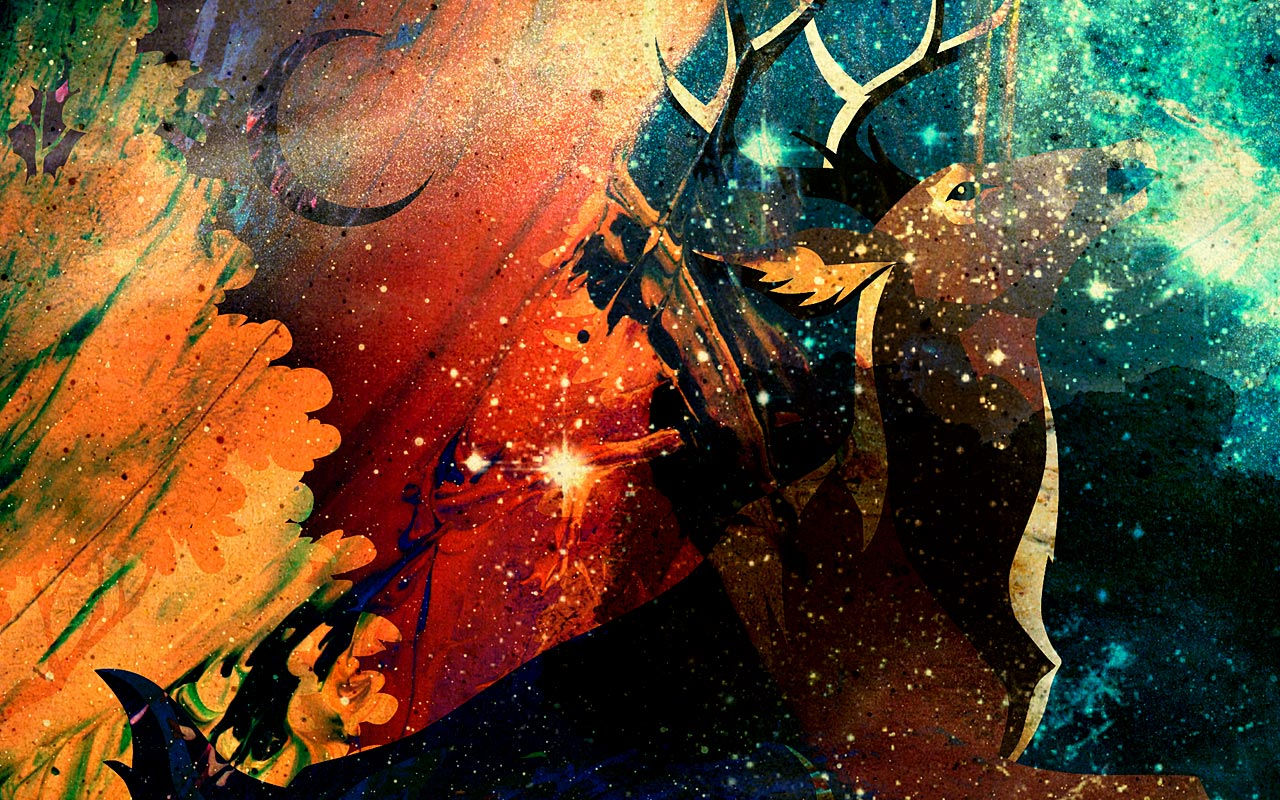
Fibreglass
Fibreglass is an crucial technique to master as it is used very often in the industry to make moulds of sculpts and manyother materials. The process can be potentially very dangerous and must be approached with care as to not cause any accidents or waste materials. Once mastered is a very effective way to create moulds for running many various pieces and is used in the industry at very high levels. Fibreglass moulds can be resused many times making them cost effective and efficient, however if completed incorrectly is useless and all the previous work created beforehand may be unuseable.
Fibreglass Demonstration
We received a demonstration on the process of creating a fibreglass mould, the process, materials and photographs of the process are shown below.
![]() Initial SculptFirst there needs to be a sculpt or item that you wish to mould using fibreglass. This should have grounding placed around it with keys cut into the clay, this will be the location for the holes in which the screws will be placed. Make sure that there is an even spacing between the keys and they are placed in strategic areas of the design. | ![]() ComponentsWhen making the fibreglass mould, gather all the ingredients and necessary components before starting. Make sure to have everything clear and neatly laid out for easy access. This will help with the smooth running of the process. | ![]() ComponentsTheses are the resins available in the moulding room, there are scales in order to measure the materials accurately. The black container is the desired resin for the use in our fibreglass moulds. |
---|---|---|
![]() Resin and CatalystAfter combining the catalyst with the resin the mixture will slowly change to become a blue colour, this will inform when the two elements have been thoroughly mixed together and are ready for use. The colour will change from pink to a blue/grey colour. | ![]() ResinMixing the resin and the catalyst, the colour of the mixture will change when the catalyst has been thoroughly mixed in. At first the resin will be coloured pinkish. | ![]() Fibreglass SheetsThis sheet of fibreglass has thick, strong strands of glass, this is used for the first layer of the fibreglass mould. The interlocking shards of glass create a strong structure and therefore are particularly strong for use in the mould. However as the shards are larger it means that the final result of the mould will look rough unless covered by finer fibreglass. |
![]() Fibreglass SheetsThese sheets of fibreglass are the finer glass, pulled thinner and are used to finish off the mould and create an aesthetically pleasing mould. This is an important step in the process as you want to create a mould that shows that you care about the work you create. It therefore will look more professional. | ![]() Applying the filler gelif there are any undercuts in the sculpt a thicker gel should be applied as this will fill the area preventing the mould from locking when set. To make this mixture simply add talcum powder to the resing and catalyst mixture and mix thoroughly. apply this with a spatula or chip brush to any undercuts and the keys in the grounding as these could also cause locking if not filled properly. | ![]() Applying the Gel CoatTo ensure that all the detail of the sculpt is picked up in the mould a layer of gel coat must be applied. This gel is a mixture of resin and catalyst.It should be applied all of the sculpt and the grounding making sure that there are no areas without this coat. It sets in around 30 minutes, however you want to begin applying the fibreglass before it is fully dry in order that they adhere together. |
![]() Applying Resin to FibreglassTo break down the starch in the fibreglass sheets use the resin and catalyst mixture and apply to the sheet. Allow to sink in for a minute or so this will make the piece easier to apply to the mould. | ![]() Applying the FibreglassUsing more of the resin apply the fibreglass sheets to the sculpt. Place the sheet on the sculpt and use the resin to smooth it on, make sure that there are no air bubbles underneath the sheet as this will weaken and potentially ruin the casting process. Make sure the resin is thoroughly applied and the sheet is properly smoothed out. Complete 2-3 layers of this process to get a good thikness to the mould. | ![]() Applying the FibreglassOnce the layer of thick fibreglass has been applied to the sculpt, to finish off the whole mould apply a layer of the finer fibreglass with a smoother surface, this will make the final outcome much more aesthetically pleasing and look professional. |
![]() Applying the FibreglassMake sure to apply the fibreglass sheets over the entire mould, this will give a smooth finish. Use large amounts of resin to create a detailed, smooth effect, always making sure to remove any air bubbles as this could cause problems further down the process and it will look unappealing. |
![]() IMG_7028.JPG | ![]() Components of Mould MakingBefore I began creating the fibreglass mould I collected all the components in order that I was not rushed and remembered every step. I cut the fibreglass neatly as I wanted to create a finish that looked neat and worked successfully. | ![]() Applying the Gel CoatTo prep the mould I applied mould release to the plastic vacuum formed face to prevent it sticking to the fibreglass. The first step was to apply the gel coat to my sculpt, I began this by mixing the resin and catalyst thoroughly and applying it to the sculpt with a woodchip brush. I made sure to apply the coat evenly over the entire sculpt so as to pick up all the detail. |
---|---|---|
![]() Applying the Thickened ResinAs my sculpt had significant undercuts under the eyebrows I need to fill this with the thickened resin. To create this mixture you combine talcum powder with the resin and catalyst, this can be pasted onto the sculpt. I should have added more talcum powder to make a thicker paste as it was runny when I applied it to the sculpt. However it still held and worked well fo the mould. | ![]() Applying the FibreglassThe next stage was to apply the thicker fibreglass using resin and catalyst. I made sure that there was a large amount of resin to fully ensure the fibreglass held tightly to the mould and there were no air bubbles in the mould. I was very happy with the application as it looked very neat on the outside and had no air bubblesbetween the layers. | ![]() Final Fibreglass MouldThis photograph shows the final result of the fibreglass mould, I am very pleased with the results, as you can see there are no air bubbles and very little excess fibreglass shard around the bottom of the mould. |
![]() Final Fibreglass MouldHere I can see that there was perhaps slightly less fibreglass around the edges of the mould, however there were still at least two layers. Overall I was very happy with the result of the mould for a first attempt. | ![]() Drilling Holes in the MouldHere there are two of the holes that I drilled in the mould to attach the screws which will hold the two components together when I pour my casting material into the mould. I did these very carefully as I knew that the holes would fragment if I did the drilling on a setting too fast or pressed too hard. I also tried to keep them at 90 degrees to the mould to make a smooth entry for the screws. | ![]() Drilling Holes in the MouldHere are some more of the drilled holes around the edge of the mould. I found it very difficult to place the holes as I could not see clearly where the keys in the grounding were placed. In one instance I drilled through the clay which meant that the core and the mould would not fit together when screwed which could potentially cause issues with the casting process. |
![]() Sawing the Excess Fibreglassunfortunately I do not have a photograph of myself doing this process however I used a vibrosaw to cut the excess fibrglass shards off of the mould as they could be potential hazard and the finish is therefore smoother and professional. | ![]() Sanding down the EdgesAfter sawing off the shards of fibreglass I began to sand down the edges of the mould to create a smooth edge and polish off the final result. I was very happy with the result of this as it made the overall fibreglass piece look much more impressive and neat. | ![]() Colouration of the SiliconeThe first attempt at creating a piece through the use of a fibreglass mould was to cast it in silicone. This proved much more challenging than I had originally thought it would be. I mised these two colours into the silicone to give it a space age, futuristic alien vibe, with a slight translucency. |
![]() Final Result - SiliconeI poured the silicone into the mould after previously applying many layers of cap plastic and bolted the mould shut with screws to ensure that it held together tightly. I only found upon opening the mould that I had use way too little silicone and it had pooled in the centre of the head. I had also not closed the mould tightly enough as the silicone went all the way around the edge where the flashing was intended to be. However I have learnt from my mistakes for next time. | ![]() The Mould after removal of ScrewsI did not take a photograph of the mould with all of the screws in place, however I did before removal of the core from the mould. Some of the silicone had poured out wasting some material. I also found that the process of winding the bolts onto the screws was very time consuming and meant that the silicone had begun curing by the time they were all attached which will need adjusting for the next trial. |
Fibreglassing is an important technique to understand as it will create durable and substantial moulds that can be used many times with the core, which similarly can be made out of fibreglass for a long lasting base. Special Makeup Effects, T.Debreceni states the important of safety procedures that must be implimented when creating a fibreglass mould. Debreceni reiterates many times the necessity of making sure that the environment in which the moulds are created is safe and fully equipped and the mould-maker has all the personal safety equipment required.
To be safe in a fibreglass room, everything must be completed carefully, with thought put into each process. The room must be well ventilated in order to remove the harmful materials which are released during the process. There should be fire hazard precaution available and in close proximity. Personal safety equipment involves wearing a respirator, which will filter out any harmful materials or substances that are airborne. It is recommended that a mould-maker wears protective clothing such as overalls as these protect the skin and can be pulled off quickly if a product is spilled onto them. Gloves can also be worn to try and prvent fibreglass splinters from hurting your hands, however these cannot be latex gloves, they must be Nitril or Vinyl based. It is important to be vigile and constantly aware of your environment when creating a fibreglass mould, this is probably the most important thing to consider. Use common sense and be aware.
Creating My Fibreglass Mould
There is a video created by Stuart Bray at Learn Makeup Effects detailing the process of creating a fibreglass mould. There are elements involved that were not used in the creation of the second fibreglass mould, however would be worth considering when creating another piece as the logic behind the process makes sense and may produce a more detailed result. The videos created by Bray are very helpful as they give a visual aid as to the processes described in books, and show every element clearly stating every element included. If it is necessary to create another fibreglass mould for this projecct using the technique of using small fibrglass chips, as seen in the screenshot of the video to ensure that the detail is picked up. This is important as the first layer of the fibreglass is the closest to the sculpt.
Stuart Bray (2012) Using Fibreglass Part 1 [Online] Available From: https://www.youtube.com/watch?v=gMOvEnjvaZg#t=746 Date Accessed: 15/01/2015
Materials
As mentioned in the process of creating a fibreglass mould which is shown above it is important to know and have all of the necessary materials available for use. Therefore I have made a list of the products and their definitions from Special Makeup Effects, T.Debreceni (2009).
Fibreglass - A material consisting of extremely fine glass fibres suspended in a polymer resin, used in making various products, such as yarns, fabrics, insulators and structural objects or parts. An excellent mould material, extremely strong and lightweight.
- Fibreglass Mat - A coarser, stronger material than cloth, has bigger shards of fibreglass, creates a strong base, however the finish is not aesthetically pleasing. Mat, is loose and disorganised which makes it stronger than cloth.
- Fibreglass Cloth/ Veil - A fine material, the fibreglass is much finer and delicate, provides a much smoother finish, can be used to finish off a mould or for use in a situation where only a small mould is being made. The strands of glass are neatly woven and do not intermesh.
Fiberglass is a strong lightweight material and is used for many products. Although it is not as strong and stiff as composites based on carbon fiber, it is less brittle, and its raw materials are much cheaper. Its bulk strength and weight are also better than many metals, and it can be more readily molded into complex shapes. Applications of fiberglass include:
Aircraft • Boats • Automobiles • Bath tubs and enclosures • Septic tanks • Water tanks • Roofing • Mould making
Lamminating Resin - Resin is used to breakdown the fibreglass sheets for application. It contains styrene which softens the cloth and mat, to make it pliable and mouldable. Styrene is the main reason for the ventilation precautions .
Gel Coat Resin - A thick polymer resin coat used in fibreglass fabrication; the gel coat is used as a detail or brush-up layer before applying resin and fibreglass mat or fibreglass cloth as strength layers.
Catalyst (Benzoyl Peroxide) - Methyl Ethyl Ketone Peroxide (MEKP), Organic Peroxide. 2% Catalyst should be added to the Gel Coat Resin and Lamminating Resin to begin the reaction.
Loose Chopped Strands (Choppies) - Loose strands of fibreglass that can be used for a fine detail layer before applying the matting.
Lay Up Resin - One of a group of synthetic resins that undergoes polymerization during curing. It has excellent adhesive properties, high strength, good chemical resistance; esp. used in laminating
(Tindall.P. (N.D) Processing silicone prosthetic - Using Fibreglass (GRP) [PDF] Available From: https://mycourse.aub.ac.uk/fdmse/files/2011/09/Processing-silicone-prosthetics.pdf Date Accessed: 15/01/2015)
These are the primary materials used in the creation of a mould, however there are other materials involved such as talcum powder and petroleum jelly. It is important in everything that is done to fully understand the materials being used as there could be errors in judgement which could seriously harm a person or create a dangerous situation. Full understanding is a requirement in order to work safely and effectively.

It is important to know which filters block out certain harmful gasses as the gases which are being used may not be filtered out through the respirator, therefore potentially causing a harmful effect to the wearer. This chart shows the coding for the respirators and the gases which are prevented from causing harm.
Fibreglassing the Lifecast
After taking a lifecast in silicone it is possible to fibreglass directly into the negative, this will produce a fibreglass positive of the model's face. This means that the process of creating a fibreglass positive is massively reduced saving on time and materials. To create a fibreglass positive from a silicone mould the gel coat should be applied directly into the negative, this was pigmented blue in order to allow easy visibility when sculpting. While fibreglassing in order to have easy removal a wooden bar was placed in the back of the positive, this can be used when the other element of the mould has been created and the piece is being run. The process is described with photographs below.
![]() Prying the Fibreglass ApartThe fibreglass and silicone parts would not come away from each other after being moulded, therefore it was necessary to try and place wooden sticks down the edges in order to get leverage and pull the two apart.This whole process proved much more challenging that originally thought but eventually gave way. | ![]() Silicone MouldThis is the outer side of the silicone mould after being fibreglassed into. It looks relatively rough, however this is due to the gravity when being applied to the face. | ![]() Silicone and Plaster MouldThese are the two halves of the positive mould, the silicone detail layer and the plaster outer layer to hold the structure of the silicone while being moulded. These two elements came apart in the process of taking the fireglass out, the edges of the plaster were buckled slightly due to the pressure applied. |
---|---|---|
![]() Plaster ShellThis is the plaster shell after removal, the edges were slightly damaged in the process, however I think the overall neatness of the plaster looked professional and neat. | ![]() Fibreglass FaceThis is the fibreglass core after removal from the silicone and plaster shell, the result looked quite effective. However there were quite a few bubbles and the nose was slightly distorted, however I think the final result looked very neat. | ![]() Fibreglass FaceThe core was pigmented blue through the gel coat layer, in order for the sculpt to be seen easily, as if the coat had not been pigmented it would be a brown colour which would prove difficult to sculpt on and hard to seen the edges to ensure that they are thin enough. |
![]() Smoothing the SurfaceAs the fibreglass positive came out with quite a few bubbles it was necessary to smooth out the surface to get a surface on which to sculpt successfully. To complete this task the dremmel tool was used. It is a small rock-like material that spins, it can be used to sand off the excess maerial found on the lifecast. The result of this technique is quite effective and worked well, producing a successful result. | ![]() Creating NostrilsThe nostrils were slightly distorted in the process and therefore needed to be dremmeled inwards in order to create a realistic nose which can be sculpted around. This is a process that requires small movements in order to not ruin the fibreglass and take off too much material. The corners of the lips also required sanding and therefore the dremmel was an effective tool, however it revealed an air bubble under the right corner and therefore needed a new batch of gel coat to fill it in. | ![]() Gel Coat LayerThis photograph shows the first coat of gel coat, it was applied in a relatively thin layer all over the face. This ensured that all the detail from the sculpt was picked up. |
![]() FibreglassingThis photograph shows the materials collected, also the thicker layer of gel coat that was applied to the face, It looks messy, however it was to ensure that there were no undercuts, and this layer will not be seen after removal from the positive as it will be between the fibreglass and first gel coat layer. It is important to be as neat as possible in order to create the most professional result and take pride in ones work. | ![]() Final FibreglassThis is the final result of the fibreglassing, it is quite neat and looks professional. This therefore means that it will aesthetically look pleasing. There was no veil fibreglass available in workshop therefore the outer edge will not be as smooth and may have a slight shard-like look. |
![]() Creating a Fibreglass Two Part MouldIn this photograph the wall of wet clay has been built around the silicone piece with keys, cut into the clay. These were strategically placed evenly to ensure a neat finish that locks together well. The gel coat has been applied in this photograph, to ensure the detail of the keys has been picked up to fit perfectly together with the other half when fibreglassed. | ![]() Creating a Fibreglass Two Part MouldThis is the final result of the fibreglassing process with the bolts screwed in place. The edges of the two pieces have been sanded so that they fit perfectly together. The bolts have also been placed strategically to ensure even pressure over the piece. With bolts close to the ends as these will be the weakest points on the mould. | ![]() Creating a Fibreglass Two Part MouldThis shows the fibreglass from close up, the veil fibreglass was available when creating this piece, therefore giving the final finish a smooth shell. The veil makes the pieces look pleasing and also prevents any rough fibreglass shards from lifting causing injury. |
---|---|---|
![]() Creating a Fibreglass Two Part MouldThis photograph shows the fibreglass mould with the silicone inside from the bottom. Although the joining edges are not perfectly straight the fit together well, it means the the silicone fits well creating an effective mould. Overall the result of the fibreglass is very successful and has proved effective. |
Creating a Fibreglass Two Part Mould
As the plaster mould for the spines did not work, it was necessary to create another suitable mould that would hold the silicone spine moulds, whilst be cast with the fast cast resin. To do this a fibreglass mould was created using two parts the bolt together holding the silicone in place securely. This fibreglass piece was created by building a wall of wet clay around the silicone mould to create a flat surface onto which the fibreglass could be layed. This ensured that there were no overlaps and the two halves did not lock together. This wall can be seen in the first photograph, It was also necessary to create keys for the fibrglass to slot into after being pulled apart. This mould worked particularly well when holding the silicone in place, it also looks very aesthetically pleasing. The outside of the mould is smooth and neat, the edges have been sanded down to create a good edge that fits perfectly over the other piece. Overall the result of this piece was very effective and fulfilled its criteria for useage well, and will be strong enough for multiple uses.
Examples of Professional Fibreglass Moulds
![]() Clay Wall + First FibreglassThis tutorial from Learn Makeup Effects shows the process of creating a fibreglass mould through the use of photographs. This is the initial stage in the process, building up the wall around the sculpt. Covering the sculpt with gel coat and applying the fibreglass to create the first half of the mould. | ![]() Fibreglass Mould Clay removedThis photograph shows the first half of the mould after removal of the wet clay wall. There are small keys in the fibreglass to ensure that the two halves match up when placed together. This is a good tip to use when creating a two part fibreglass mould. I will create these on the mould of the spines to ensure they match up perfectly. | ![]() Final Fbreglass MouldThis photograph shows the application of the second half of the mould. The two halves match up perfectly with a very smooth edge. The overall finish of this mould is very professional looking. It is important to take pride in the mould work as these mould could be reused multiple times. |
---|---|---|
![]() Cleaning out FibreglassHere is the core and the negative after removal from each other. It is important to clean out the mould very thoroughly to ensure that when the piece is run the material picks up all the necessary detail of the sculpt. | ![]() Casting in the fibreglass MouldThis photograhp shows the two halves of the fibreglass bolted together around the core, with the casting material being injected into the head. This mould is one to look to for inspiration and direction as to creating a neat and effective mould. | ![]() Wolfman MouldThis fibreglass mould uses multiple pieces to create a smooth finish that ensures that the piece is run well with little damage. All the individual elements are bolted together and the casting material is injected into the mould. Creating the mould in multiple small pieces allows easy removal after casting the piece, it means that the piece wont be damaged when trying to get into the awkward areas of the piece. |
Fibreglass Mould (2013)[Online Image] Available From: http://www.learnmakeupeffects.com/blog/page/2/ Date Accessed: 25/02/2015