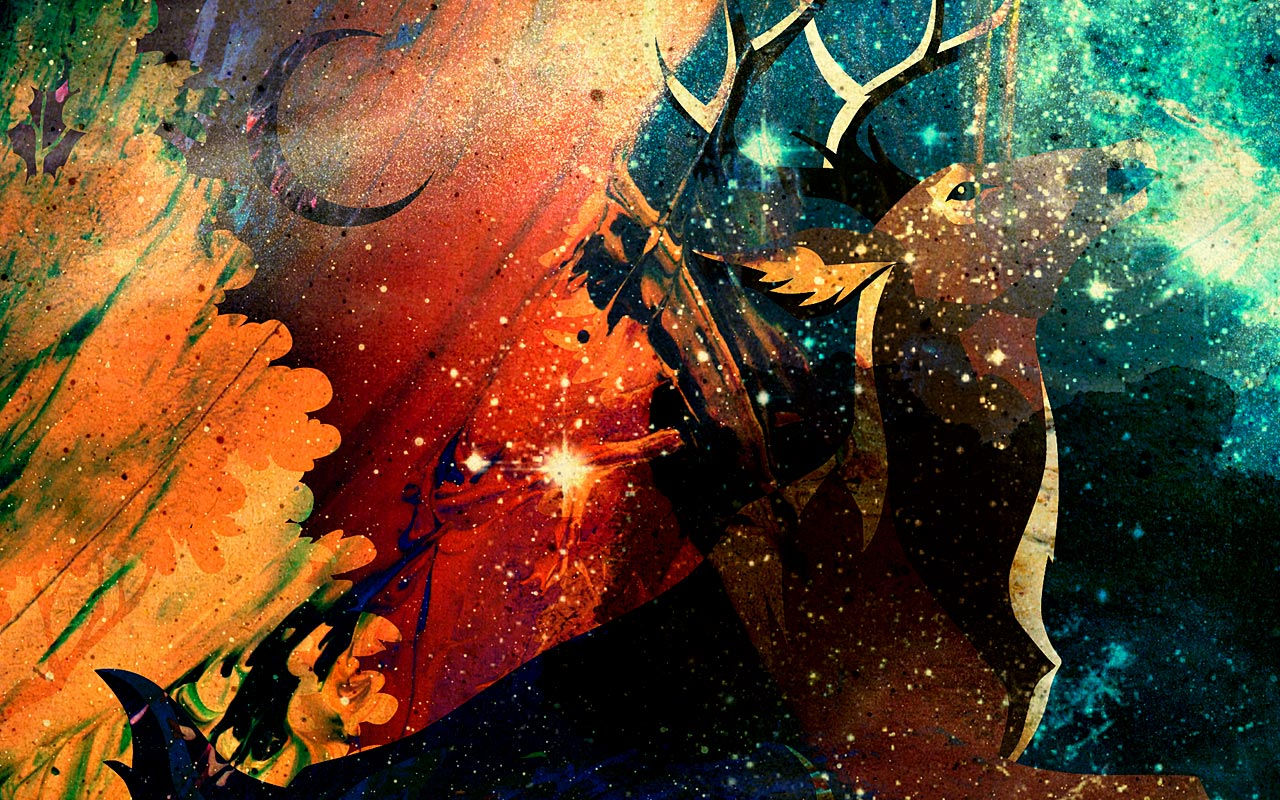
Moulding
There are many processes in the creation of prosthetics and moulding is by far one of the most crucial. If a mould is made correctly and effectively it may be used to run a cast multiple times before the detailing and material wears out. However if a mould is made badly it will ruin any previous work completed, such as the sculpt and positive of the model deeming these both unuseable. In the makeup industry it is generalised that a trainee will begin their work in the mould room therefore it is highly important that the technique is fully understood. There are many different types of mould that can be created for different purposes, from silicone flatpiece moulds to plaster compression moulds to fibreglass moulds and various others. The first moulding technique is creating silicone flatpiece moulds.
To begin to create a mould from silicone the first step is to create the sculpt or choose your desired product to mould and create a negative in which materials can be cast. Once the item has been selected the first stage is to lubricate the item with product (vaseline/mould release/mould wax) this will prevent the item from attaching itself to the silicone and make sure that the final result is accurate. A wall must be built around the desired item for moulding in order to prevent the silicone from running and not moulding the object successfully. The wall can be made from clay moulded around the sculpt or a container can be used with the item placed inside, there are many methodologies that can be used it does not necessarily matter what is used as a wall as long as it holds the silicone whilst it sets. Next the silicone must be measured accurately in order to get a successful final result. For the mould equal parts of the two part silicone must be weighed. Popular moulding silicones include Platsil Gel and Pro Gel these are both two part materials once mixed together will cure and form a strong silicone piece in which other materials can be applied for moulding. Once the two parts of silicone are combined the working time is roughly 3-5 minutes therefore there is enough time to not rush, however it is essential to move quickly in order to create a successful mould. To pour the silicone into the mould it should be held at a high height and slowly poured in a very thin stream as this will remove any air bubbles from the mixture. Pour directly onto the centre of the item being moulded in order for the material to naturally work its way into any crevaces and details. Once the mixture is poured leave on a flat surface for 30 minutes and the silicone should have set into a firm but flexible piece. The final result of pouring silicone into a sculpt can be seen in the first image below. The silicone has set into a slightly opaque coloured piece.





A complete Guide to Special Effects Makeup gives a brief and simplified version of creating a mould for creating prosthetics. It states that 'Mould making constitutes the most critical element of specail effects makeup. Once you are able to create moulds, you will be able to produce arresting special effects makeup that fits snugly against the wearer's skin'. These photographs below highlight the basic creation of a mould exluding the specifics of various materials that can be used to create the prosthetic pieces. It conducts the mould making process as though Foam Latex is being used in the mould as an example however Silicone, Gelatin or many other products can be used to create these pieces.
![]() Nose Sculpt (After Moulding)This photograph shows my sculpt of the nose after moulding, I was very happy with the way it was sculpted, it resembled the nose in my portrait well and had edges that were not in the generic place in order to pull the eye away from where the edge is supposed to be. I also made sure to not use too much material to keep it thin to create a big difference to the face without too much attention being drawn to the prosthetic pieces. | ![]() Nose MouldThis was the final result of my mould, I had to complete the mould quickly as I was running out of time during the day and needed to run the piece the next therefore I am not as a happy with the result as I would have liked it to be. I would like to have spent a bit more time slowly layering up the plaster to get a neat cast from bottom to top and make sure all the areas of the mould were properly filled. | ![]() Nose MouldThis shows the mould from the side angle, I would have liked the shape of the mould to have been much more symmetrical with less rough edges, however overall I am quite happy with the outer portion of this mould. |
---|---|---|
![]() Nose MouldFrom this angle I can see the corner which cause some problems inside the sculpt there is an air pocket to the right hand side around the flashing and the angle of the outer mould meant that when pouring the silicone it rocked slightly making it difficult to hold steady. | ![]() Fixing the NoseI found upon removal of my sculpt after moulding that there was a small lump of unmixed plaster in the nose which I therefore needed to patch up before casting the silicone in the mould. To fix this problem I dug out a small hole where the unmixed plaster was with a lip over the edge in order to apply a small amount of plaster to the cast without it coming loose. I made sure that the edges were smooth so that when I cast my nose it fits my model perfectly. | ![]() Inside Nose MouldFrom the inside the rushed moulding can be seen clearer, there was a few air pockets around the flashing, although this does not affect the sculpt I am not happy with the poor result of this section of the mould. The edges of the whole piece have since been smoothed down to get a better finish. |
![]() Inside Nose MouldThis is result of my negative mould, the piece ran well, however there were a couple of chipped pieces around the flashing that may cause the edges of my silicone piece to run thick. I therefore glued all the elements that I could find in order to try and prevent this from occurring. | ![]() Inside Nose MouldAs the nose sculpt went around the edge of my lifecasts nose it was necessary for me to place a small piece of clay in the corners to prevent the mould from locking, however this meant the the mould had a slight bump in the flashing that will collect silicone when poured. Overall there were glitches in this mould, however I think the final result was successful enough to make a good piece for application. I would like to practice making moulds to make sure that the sculpts come out perfectly. |
![]() LifecastI initially had some issues removing the lifecast from the mould as they locked slightly, during the process of trying to remove the cast I pulled off the extra base that I had attached to give stability and to allow me to sculpt the pieces with enough room for creating grounding. As this occurred it meant that I had to chisel away some of the mould in order to get a grasp on the cast to pull it off the mould. This photograph shows the part that I removed. | ![]() Creating Overflow ChannelsDuring the sculpting process of the second nose I forgot to attach overflow channels to the grounding meaning that if I poured too much silicone or gelatin into the mould it would stay trapped inside causing the nose to have very thick edges. I therefore created these channels myself in the plaster rather than resculpting and moulding the piece to save on time. | ![]() Creating Overflow ChannelsThis photograph shows a close up of one of the channels that I created for the excess material. To create these channels I used a strong sculpting tool and carefully scraped away at the plaster. This worked very successfully, the edges were clean and I managed to make a smooth finish that worked effectively. |
---|---|---|
![]() Creating Overflow ChannelsThis photograph shows the final result of creating the overflow channels, I believe that I managed to create effective segments in the plaster that look neat and will work well when the material is poured in to create the closed mould prosthetic. |
Second Nose Mould
After feedback on my formative assessment my lecturer noted that the nose was too bulbous at the tip of the nose, I therefroe decided that it was necessary to re-sculpt and mould the nose. I also felt that I could create a more successfuly mould that had no air bubbles and chips that would affect the result of the prosthetics created from it. Recreating the nose and mould would also give me more experience in this area therefore improving my skill allowing me to get a better understanding of the concept and create better moulds in the future. These photographs below detail the mould-making process of my second nose.
![]() Sculpt and GroundingTo create my first negative mould for the mould making process I began by sculpting a nose onto a generic plaster face, detailing and making sure that it looks realistic. I then created the grounding for the piece. To do so I made a clay edge around the nose following closely to the shape of the sculpt. I then added keys (the small holes) to ensure the negative would fit perfectly to the positive. I finally added some overflow points to ensure that any excess material is removed. | ![]() Mixing the PlasterTo ensure that I got a smooth application of plaster to create the mould I mixed a large amount of plaster into water to get a thick substance. I made sure to remove all lumps of plaster as this could cause problems in the mould at a later point in the process. | ![]() Applying the Plaster MouldTo apply the plaster to the nose I used a brush as this allowed me to get into the crevices of the mould making sure that there were no trapped air bubbles that would cause an issue with the final mould. I slowly applied the plaster building up the layers as it set to create a strong structured mould. |
---|---|---|
![]() Applying the Plaster MouldAt this stage in the process the plaster was getting thicker so I was able to build up the height to create a strong structure that would not chip and destroy the mould. I slowly built up the plaster to ensure there was an inch of plaster around every point of the sculpt for security. | ![]() Applying the Plaster MouldThe final stage of the process was to smooth off the plaster in order for a neat finish and to be able to lay the mould flat on a surface whilst pouring the material that I would use for the prosthetics without issue. It also shows pride in my work to have a successful aesthetically pleasing mould. | ![]() Final MouldThis was the result of the mould making process, the stage after releasing the two halves. I was very happy with the way it turned out as there were no air pockets and the edges were held together well, no area was chipped and the nose fit perfectly back over the generic nose cast once all the clay was removed. |
![]() Aplying Gelatin to MouldTo experiment with creating negative moulds I poured gelatin into the cast and applied pressure with weights to make sure that all the excess was pushed into the overflow areas in the mould. This photograph shows my first attempt whilst still in the mould, it is visible that I did not use enough gelatin to fill the outer ring of the mould and therefore it was difficult to remove the nose whilst keeping all of the flashing attached. | ![]() Gelatin Nose First AttemptThis photograph shows the nose cast in gelatin once removed from the mould. There is little to no flashing around the edges of the nose and only a small area as the top to hold on to whilst applying. The mould itself worked well, there were no air bubbles and the piece was smooth and the edges were thin. However I decided to run the piece again to get the extra flashing and edging to hold on to. | ![]() Gelatin Nose Second AttemptThis is the nose on second attempt with a little talcum powder on the top. The flashing and edges worked much more successfully on this piece giving me a full 360 degree edge to hold onto whilst applying. The nose had no air bubbles and had a smooth finish.To improve on this piece I will try to add colour to the gelatin to give it a more flesh-like result that will apply more successfully. |
The next step in the mould making process is to create the prosthetic for application. To create a simple silicone prosthetic flatpiece the process is relatively simple. First begin by applying vaseline/mould wax/mould release to the mould allowing it to fully dry. Then apply four or five layers of cap plastic mixted with 99% isopropyl alcohol in a ratio of 1:3, allowing each layer to fully set. The next stage is to pour the silicone.
There are three parts to making a silicone piece the first two are parts A + B of the silicone being used. This must be measured in equal amounts to each other. The third is the deadener/softerner this must be measured to equal the same weight as parts A + B combined to create a 100% deadened mixture. This will create a flesh-like texture. Silicone pigment and flocking must then be added to make a flesh colour. very small amounts of pigment are needed as it creates an opaque colour if used too much whereas skin is slightly translucent. To make sure the right amount of pigment is used, colour a small black dot on a mixing stick and dip it in the silicone and hold it up as it pours off the stick, the dot should not be visible for a couple of seconds and then slowly appear. This is the stage when the silicone is coloured to the correct amount. The flocking adds texture to the prosthetic breaking up the colouring making the final result more realistic. To create a skin colour red flocking is used with a light, beige coloured pigment. The silicone must then be poured from a height into the mould to remove any bubbles from the mixture filling the mould itself and the wall around it. The next stage is to scrape the excess silicone away leaving the wall and mould filled with no silicone around the edges to allow for flashing which will allow for easy application. Once set apply four or five more layers of the cap plastic mixture, allow to set and powder. When peeling away from the mould make sure to powder thoroughly to prevent the cap plastic from sticking to itself.
The photographs above display the process just described for creating a silicone flatpiece.
To deaden silicone there is a scale called the Shore Hardness Scale it depcits the type of silicone found at the different areas of the scale. I have included an image of the scale below to give an idea of the substances found at different points. To deaden silicone it will give different varieties of texture, soft or hard this can be very useful when creating a prosthetic piece as it will hold different textures in different areas of the face for example the nose is much harder than the cheek.
To run the materials in the mould it depends on which are being used as to the approach to take when creating a closed mould piece. As seen earlier on the page creating a gelatin appliance is realtively simple, it is just a matter of using a mould release, heating the gelatin, pouring it in and compressing the cast in. To create a silicone appliance is a slightly stretched out process, however still simple.
To begin there must be a layer of vaseline, mould wax or mould release thoroughly applied to the plaster in order to prevent the cap plastic from sticking. Once applied and left to dry/set the first layer of cap plastic can be applied, the cap plastic is combined with 99% isopropyl alcohol in a ratio of 1:3. This is applied with a brush to get into the crevacies and any area of the mould. This must then be left to dry fully and three of four more layers should then be applied. I found at this stage in the process that small puddles of the mixture were forming in natural dips in the mould and were not setting, no matter the length of time left for. Therefore it is important to make sure that any excess is removed, I found that placing the mould on its head with the top of the nose facing downwards allowed the excess to flow out of the tip of the nose and into the grounding area which does not matter as much. Once the cap plastic is fully applied the next step is to pour the silicone.
For the silicone it must be mixed with deadener to create a soft, flesh-like texture. For this nose it was done in equal measure to the silicone used thereofre making the silicone 100% deadened. This means that the amount of parts A + B combined, were equal to the amount of deadener used. Once correctly mixed it must be poured into the nose from a height in order to remove any bubbles created from the mixing. Pour enough to fill the nose and the grounding area as this will provide a strong support for the nose whilst applying. The lifecast should be quickly compressed into the mould tightly forcing the excess silicone out of the nasal area and into the overflow channels. This will ensure that the edges on the nose are thin and therefore blendable. Whilst the silicone is setting place a heavy object on top of the cast or use a compression belt to tighten the two together. Use some excess silicone to judge when it is set (it should be roughly 30 minutes) and pull apart the cast and mould. Once apart apply more layers of the cap plastic mixture over the silicone this will encapsulate the material for successfuly application. Four or Five layers should suffice. Once dry powder the top and begin to carefully prise the cap plastic and silicone away from the plaster powdering all the time until the prosthetic is fully removed.
Closed Mould Research
The Complete Makeup Artist, by P. Delamar has a very simplistic methodology of creating a closed mould, I thought it interesting to understand the various ways in which it can be completed. Delamar's process begins by filling a small plastic box with plaster, making sure the surface is flat, removing this from the box and create keys in the plaster. To create keys in the mould it says to use a small saw cut three small triangles around the edge, once complete coat the mould in vaseline or Shellac and begin sculpting the chosen design onto this plaster using WED clay. Once complete make a small wall around the piece, apply vaseline and put back into the plastic box, pressing clay around the edges. Mix some plaster and pour on top of the sculpt filling the box. Once set remove and separate the two halves, remove all of the clay and dry out the moulds in an oven (100 degrees for a minimum of two hours). After this is complete prosthetic materials can be poured into the mould.
I find that this method is very simplistic, as it is to create a simple flatpiece, which can be done more accurately with silicone as seen above. Silicone will make sure that all the detail of the sculpt is picked up and transfered into the mould. Whereas plaster may not get all of the minute details and therefore make the final prosthetic less advanced. Similarly plaster can chip easily causing it to be a fragile mould that could break easily. However I can understand that if there is not much of a budget or materials available this could be an effective way to create a prosthetic flatpiece easily and cheaply.

Shore Harness Scales (2011) [Online Image] Available From: http://www.smooth-on.com/Documents-Duromete/c1351_1370/index.html Accessed Date: 9/12/2014
Materials
Deadener
Deadener is an additice for Platsil gel or other silicones with parts A+B it will soften or 'deaden' the silicone, the more you add the softer it will be. The easiest way to describe this is if you were to add the 'A' and 'B' and cast it into a ball the ball would bounce. However if you were to add deadener to the mix at a ratio of 100% the ball would splat on the ground with only a little bounce. The more you add the less it would bounce. Once over 250% the silicone will be so soft it will be almost unmanageable.
Super Baldiez Encapsulating Plastic
Super baldiez is glue like material that can be diluted and dissolved with 99% Isopropyl alcohol. It can be sprayed into the mould prior to the silicone being added. The skin will also make a dissolvable edge to the silicone that can be seamlessly blended into the skin on application.
Silicone Pigment/Flock
Silicone pigment and flock are both for intrinsically colouring the silicone used for creating the prosthetic. They are both added prior to or during the mixing stage. The pigment is a highly concentrated colour suspended in silicone oil. As it's silicone oil-based colour it can only be used to pigment silicone. Flock is short fibre made of rayon or nylon: it comes in a multitude of colours and is added to the pigmented silicone and gives more depth and realism.