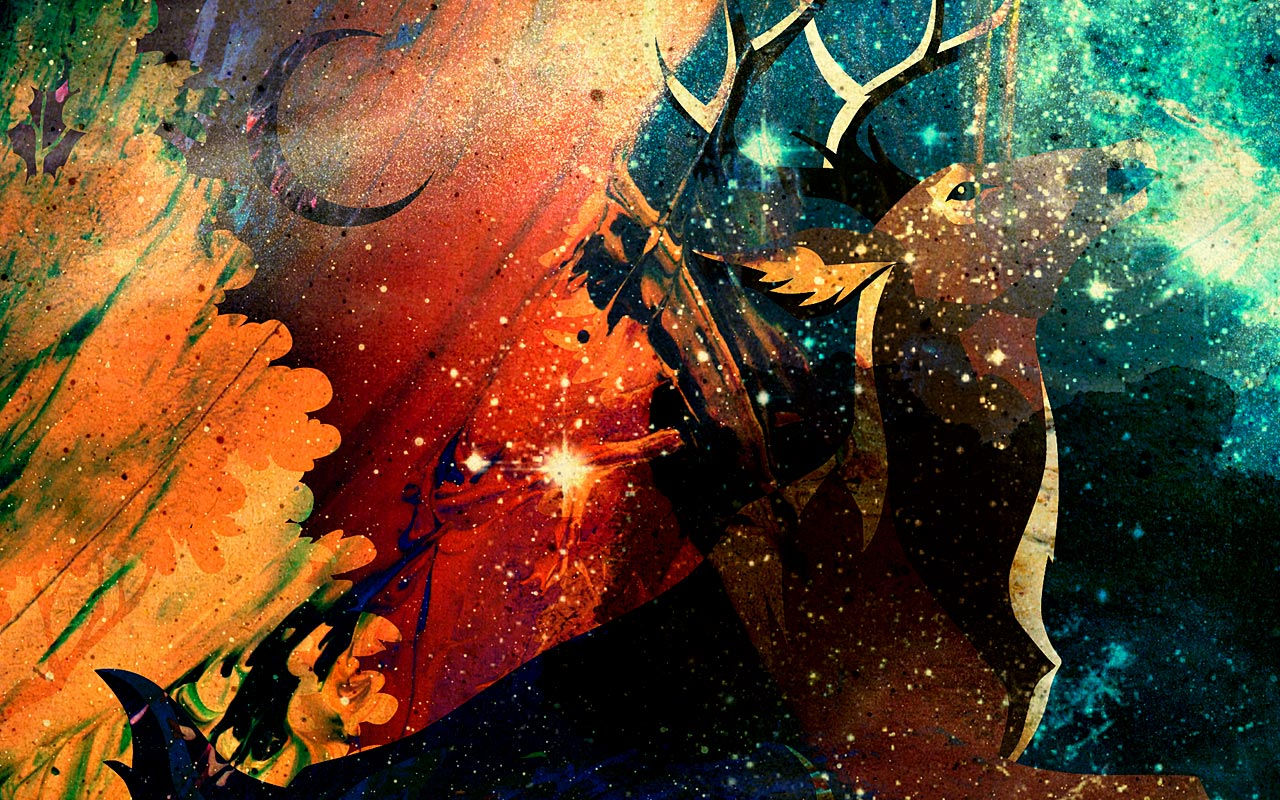
KW
Fibreglassing Lifecast
In order to create a lifecast model that can with stand the sculpting, moulding and casting process of such a big makeup it is necessary to make the lifecast in fibreglass. This will be very strong and accurate therefore allowing for repetative use. I will need to create two lifecasts as I will need to make a face and caul piece to produce a cohesive makeup. On each cast I will sculpt the front of the face and the back on the other. These will then conjoin and create a seamless prosthetic.
To create a fibreglass lifecast one must first apply the Gel Coat layer to pick up the detail layer of the sculpt, this should be applied evenly and smoothly in order to reduce the amount of air bubbles caught in the mixture and therefore make the final result smoother. Apply the gel in both halves and allow to set to tacky and place the two halves together. Then begin to lay fibreglass into the mould, this will create the tough cast of the model.
To create the fibreglass core I used the techniques that I had previously learnt when creating moulds and used my common sense in order to make the core. I as unable to find research concerning the creation of a core, therefore I asked Wayne for help and completed the core to the best of my knowledge. The result worked perfectly, I was able to create a successful core that you see below.
Wayne gave me a tutorial on how to complete the firbeglass core for the full head, suggesting techniques and tips, such as keeing the edges very neat and brushing the gel coat in so as to prevet any air bubbles from forming on the surface ruining the texture. After I had completed the core he suggested that next time I leave the matting out the sides of the core so as to prevent the folds on the inside. This will make the the adjoing edges much neater and therefore the finishing process will be reduced saving time.
Here I have photographs of the process that I completed to create my fibreglass cast. I coloured the gel coat red in order that I see the sculpt more easily. It will allow me to judge the thickness of the edges to ensure that they are perfectly smooth.
![]() Gel Coat LayerIn this photograph I have applied the Gel Coat layer to the face portion of the silicone lifecast. I ave done so with long smooth strokes so as to prevent bubbles forming on the surface leaving a smooth working surface. I ensured that the line at the base of the face was neat and smooth so that the face could stand freely, and there would be enough room for flashing around the sculpt. | ![]() Gel Coat LayerHere s the gel coat from above, I have made sure to create a very smooth line around the face so that the result of the fibreglass looks neat and professional. | ![]() Fibreglass FaceThis is the face fibreglass after removal from the silicone jacket. The face came out quite well, there were a couple of blemishes around the nose and the line of the bald cap which needed to be dremelled off. However the face worked well. |
---|---|---|
![]() Fibreglass FaceThis is the fibreglass face from the other angle, This will work very well for the face piece as the hairline is clearly marked out on the piece allowing for appropriate proportions. Similarly I have covered enough of the surrounding area to ensure that I can create a successful piece. | ![]() Fibreglass CoreThis photograph displays the two halves of the full head lifecast put together and taped with duct tape to ensure that they are held very tightly together. Before putting the halves together I had applied gelcoat to both sections and laid down two layers of thick fibreglass and one of the veil. | ![]() Fibreglass CoreI had tried to push the excess firbeglass inside the mould, which had left excess fibreglass hanging over, this is wht has created that ridge within the inside that can be seen here. After talking to Wayne I found that it is easier to leave the excess hanging out and cut these off after finishing the fibreglass. It also means that the will be no ridge in the inside of the core. I tried my best to create a smooth finish in order to prevent any injuries when putting a hand inside. |
![]() Fibreglass Core and FaceThese are the two casts, after vibrosawing the face and immediate removal from the mould of the core. They both have successful hairlines on them, allowing for matching up the prosthetic pieces. | ![]() Fibreglass CoreThis is the back of the head after removal from the plaster mould. It is quite rough, however It can be worked upon to create a smooth finish that will fit perfectly to my model's head. There needs to be a lot of work at this stage, however the fundamental shape has come out in the fibreglass allowing me to produce effective prosthetics. | ![]() Fibreglass CoreThe ears of the core did not come out of the fibreglass successfully, however after lifecasting I realised that I will not need the ears and I can therefore cover them over during final application and throughout the process. There were a few indentations in the face of the full head sculpt, however This does not matter too much, as I will not be sculpting on the face itself. |
![]() Fibreglass CoreThis shows the edge of the two halves front he side. The plaster mould fit very well together to create a successful join. However the process of folding the excess inside created a slight lip. The fibreglass looks quite rough here and needs a lot of work to produce an effective result. | ![]() Fibreglass CoreThis is a close up of the back of the head. As I had not run the back of the head in silicone it meant that the gel coat was going directly into the plaster and the surface would therefore not be neat. However it allows the fundamental shape to be made and the sanding and filling can be done to smooth it out. | ![]() Fibreglass CoreThis was the seam between the back and front after vibrosawing off the excess fibrgelass. There is quite a lip here which needed filling in order to produce a successful piece. I removed as much excess as possible at this stage, however there was still a large amount that needed removal. |
![]() Polyester Resin FillingHere I have used Polyester Filler Paste to fill in the seam along the two halves of the fibreglass mould. This is a two part paste that when mixed together has a 20 minute working time and can be applied to the subject. After this time it can be sanded down to produce a very smooth result. | ![]() Polyester Resin FillingI first began by filling the large seam between the two pieces. This can be seen here. After the setting time the paste is rock hard therefore making it suitable for filling a fibreglass mould. I layered on the polyester filler in different batches as the time frame for application was quite small. It also meant that I could produce a smoother finish filling smaller sections as I went. | ![]() Polyester Resin FillingThis is the result of the filling and sanding of the polyester filler paste. The general surface is very smooth with no large holes or blemishes. There are a few minute areas with rough surface area, however the majority of fibreglass was smoothed successfully. |
![]() Polyester Resin FillingThis shows the final result from the side to see what I had done with the ears. I covered the ears in filler paste to create a smooth surface as I had decided to cover the ears when I apply the bald cap. I left the shape there as I knew that the ears would not dissapear and would need to be accounted for in the fibreglass so as to not ruin the sculpt and the casting of the piece. | ![]() Polyester Resin FillingThis front view shows the edges have no ridge that would cause any problems with undercuts or creating the prosthetic piece. The overall result of this polyester filling has proved very successful and has a smooth result that will work extremely well with the prosthettic creation process. |