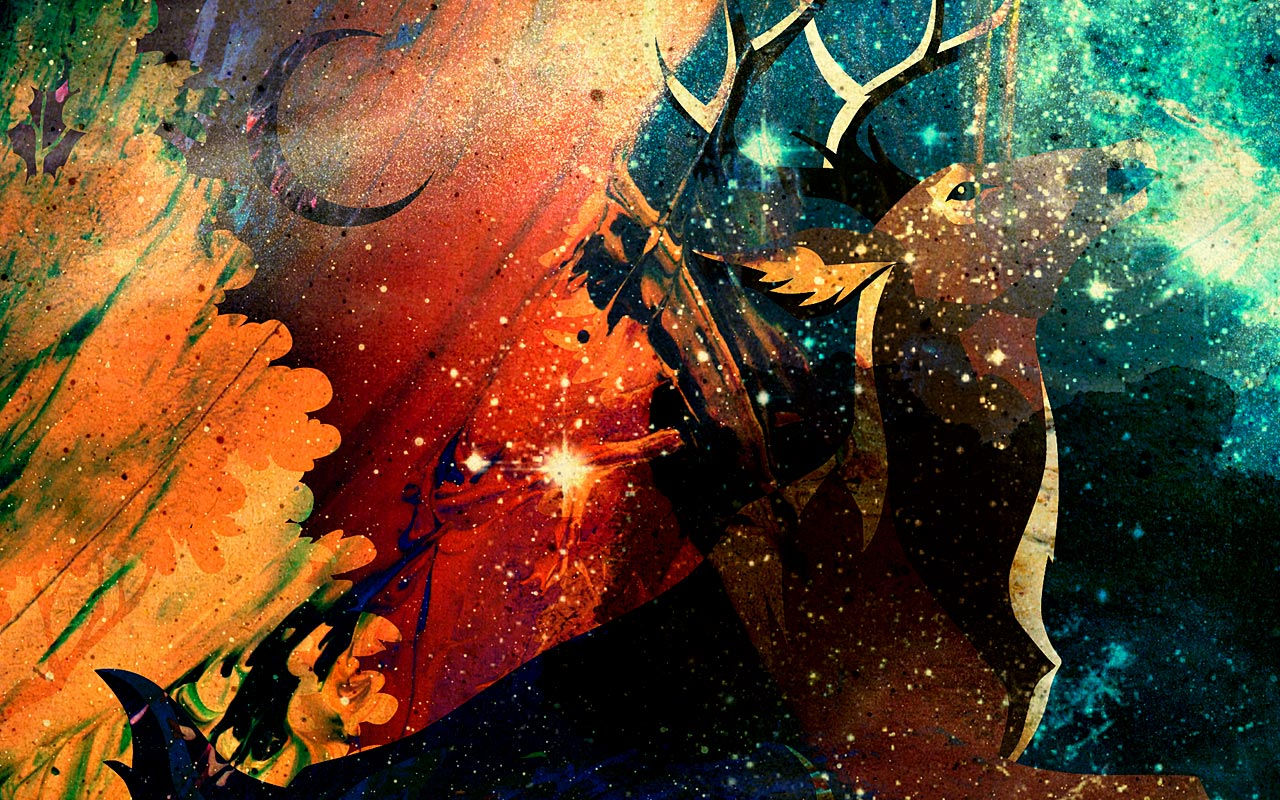
KW
Silicone
I found two very interesting articles on the uses of silicone, it is written in a colloquial tongue I therefore found that it quite easy to comprehend. I have gone through the article and coloured the important segments of the article in order to easily take note of the important factors in the process of choosing the correct silicone for the job. Although a lot of the information I knew previously it has taught me the more professional side of the products and the advanced materials that can be used. There are also many tips that are worth remembering when using silicone to make the best moulds possible.
How to Choose your Silicone:
Ok, so you have your project ready, you are off to go buy some silicone and dive right in.... Whoa! Slow down, tiger..... There is a whole bunch of stuff you need to know first.
What are you doing? Is it a big piece, a small piece? Are you making a mould or a cast? Do you need to make a box mould, a brush-up mould, a matrix mould, a pour mould? How much are you going to need to fill it? Do you want a solid coloured, or translucent silicone? Are you in a hurry or is time not an issue? Will you need a long or short Potlife? What sort of Viscosity is required? What Shore Hardness do you require in your finished piece? Do you need to worry about Elongation/Tear Strength/Tensile Strength?
Yeah, working with silicones is a bit like doing high school chemistry all over again, but trust me, if you understand the basics, it will save you a lot of time, money and frustration.
Lets start with the Product Description.
When you are searching a website for silicon moulding rubbers, you will usually find somewhere a link to a.pdf saying "Technical Data Sheet", "Product Overview", or the like. In a catalogue there may be a table giving comparisons between the products on offer.
Note that the information I am discussing here is NOT on the MSDS... (the what? I hear you say? It stands for the 'Material Safety Data Sheet'- a topic for another time...).
A Technical Data sheet will give you all of the relevant information you need about a product. Lets go through one step by step, just to give an example.
At the top there will normally be a Product Description. This will describe the general characteristics of the particular silicone, its category and type, and an idea of its texture, hardness, mix ratio and suggested applications.
Here are a couple of examples I randomly pulled out of my file (you should always keep this info for future reference):
1. "ProSkin is a two-component silicone elastomer that cures at room temperature by a polyaddition reaction that may be accelerated by heating. It is designed as a 12 Shore A high tear strength rubber providing excellent physical properties for prosthetic and orthopaedic applications. It also displays good translucency and high elongation. Proskin is easy to process with a 100:100 ratio by weight or volume and has an extremely low viscosity when mixed.
Typical Product Uses:
-
Orthopaedic Applications
-
Prosthetic Devices and appliances
-
Anywhere a soft skin-like feel is required
-
SFX skins
-
Cushioning appliances"
2. "Elastosil M4503. Pourable, condensation curing, two component silicone rubber that cures at room temperature and features:
-
Good flow
-
Low Shore A hardness (approx 25)
-
High Tear Great extensibility and elasticity
-
Excellent long term stability of the mechanical properties of the cured rubber.
-
High resistance to casting resins, particularly polyester
Applications
Due to the excellent mechanical properties of the cured rubber as well as its high resistance to casting resin, Elastosil M4503 is especially suitable for reproducing models with pronounced undercuts in casting resinc. Other materials, such as wax and plaster, may be cast without any problems in moulds made from M4503 Skin Moulds. "
Ok, so reading through those, what do they tell us? Which one is the Platinum Silicone?
Further down the sheet we come to Product Data, both Uncured and Cured. This is where the specific scientific measurements are listed. We will go through them one at a time.
No matter the format, each information sheet should have the following on it somewhere, although perhaps in a different order:
Colour
Usually translucent, white, or for certain products, blue, pink, yellow etc... Frequently, the colouring agent will be in one part, for instance the catalyst, or one part of a 1:1 system. This assists with the even mixing of the product. Proskin is a translucent silicone, that can be intrinsically coloured for the final result. This tells you that it is likely designed for making products or appliances. M4503 is a white silicone, which tells you that it is primarily used for mould making, as are most solid coloured silicones. However, there are times when you need to have a mould that is translucent, so you can see the piece through the mould itself for various reasons.
(The one thing no-one has yet managed to do is make a water-clear silicone. Well, they did, but it turned out to be so brittle it was unusable. It has since found a perfect purpose, as a form of breakable glass, too fragile to be put in a window but great for simulating crushed or broken glass on set with no danger to actors or crew).
Density, or Specific Gravity
Usually specified as @23 or similar, meaning at ambient room temperature of 23C. Density is expressed as a measure of Grams per cubic centimetre. Specific Gravity is a ratio of the Density of a substance to a reference substance, usually water. Water can be assumed to have a Density of 1 at sea level and 20C, and if a substance has a Specific Gravity of less than 1, it will float on water.
In our examples, ProSkin is listed as having a Specific Gravity of 1.08, Cured; while M4503 is listed as having a Density of 1.16, Cured. In plain terms, this translates to both kinds of silicon being heavier than water. Silicon is heavy, and fluid, and like water, follows gravity. The practical upshot of this is that if you leave a tiny hole ANYWHERE in your mould wall, or any edge is not completely sealed, the silicone will find that hole, and depending on the cure time of your material, when you come back several hours later to check on it, a great deal will have oozed out of that pinprick, and probably all over the floor.
Mix Ratio
This is not always listed as a category on its own, but will be in the information somewhere. Our examples give ProSkin a Mix Ratio of A:B 100:100. M4503 merely includes the information in the table as 'With 5% wt Catalyst T35'. Note that Proskin, a Platinum Silicone, can be measured by weight OR volume because parts A and B have been 'Specific Gravity balanced' (they are the same Density as each other).
M4503, which is Tin, must be accurately weighed. A good quality electronic scale measuring by the gram can be purchased from most kitchenware stores. If you regularly mix small quantities requiring less than 10 grams of catalyst, it is worth investing in a pocket scale that measures by the 0.1 grams.
Some silicones are very finicky and you have to get the mix ratio precisely right or it wont set at all. Others are less so, and a rough approximation will do, but its always best to get into the habit of measuring precisely for consistent results.
Pot-life
This is your active working time, and starts from the time you first put the components together in the container, including mixing time, then whatever is left is the time that the silicone is still fluid, before it becomes gel-like. It can vary substantially from what is on the sheet according to your ambient working temperature, most significantly in Platinum silicones. Potlife is generally shorter in Platinum than in Tin silicones anyway, though there is a wide range. To give you an example, I was working on a documentary in the NorthWest of Australia last year, the average temperature during the day was around 35-40 degrees Centigrade. In 24C temps, the silicone I was using, Platsil Gel10, has a potlife of around 6 minutes normally with a demould time of 30. In the tent I was working the heat was around 45 degrees Centigrade, and potlife was around 20 seconds, demould about 2 minutes....... Having a short work time is sometimes good, sometimes not!
Our Proskin has a very long potlife for a Platinum silicone, at 60 minutes, and the demould time is merely described as 'variable'. The M4503 is a fairly standard 90 minutes for Tin, with a 15-20 hour Curing Time to be tack-free.
Demould Time
This is often the single determining factor in the final choice of silicone for professionals. Have you heard of the Designers Holy Trinity? Good, Fast, Cheap. Pick Two.
If you don't have much money, but plenty of time, use Tin silicones. If you have no time, but a great deal of money, use Platinum. If you have neither, you are in trouble.
Our Proskin comes in at 'variable', which can mean anything between 30mins to a couple of hours, or less if heated to accelerate cure. M4503 will take 15-20 hours before you can touch it without it feeling sticky.
*IMPORTANT: If your silicone still feels tacky or sticky, or 'wet' on any surface after the expected cure time has elapsed, it is NOT going to set if you leave it longer. Platinum silicone can be slower in temperatures below 20C, and faster in temperatures above, or can be accelerated by application of heat (waring the mould in the oven on 50C, or blasting with a hairdryer, or directing a fan heater on it- I hasten to say, AFTER it has reached the gel stage). Tin silicone is an inexorable process that will cure in the allotted time no matter what... UNLESS there is a problem. We will be looking at possible problems later in this series.
Viscosity
This is most simply described as the relative thickness of the liquid. In actual fact it is a lot more complex, but for our purposes we don't need to get into Newtonian Fluid Mechanics..... Suffice to say that Water is measured at 1 centipoise, which is one one-hundredth of a poise, and equal to one millipascal-second (mPa·s) in System Internationale Units. Honey has a viscosity of 2 000 centipoise (or mPa s) and Molasses has a viscosity of 5 000 centipoise. Lard is extremely viscous at 100 000 centipoise. Our examples come in at 2500 mPa s for the (mixed) Proskin, and 40,000 mPa s (mixed) for the M4503.
From this we can gauge that Proskin is a really runny consistency, while the M4503 is quite thick and pasty. Can you think of situations that would require a very viscous silicone, and one that would be better with a thinner, more fluid silicone? Also remember that there are Thixotropic agents that can be added to silicones in small proportions that will change the viscosity of the material, and are often used when you need the properties of a silicon that is naturally runny (maybe because it is clear and soft) but you need to make a brush-on mould.
Hardness- (Shore #)
Probably the single most important measurement on the whole sheet. Hardness may be defined as a material's resistance to permanent indentation and is measured by a durometer, on a scale invented by Albert F Shore in 1920. There are several different scales within the system, but the most commonly used in silicone rubber technology is the ASTM D2240 type A scale, mainly used for softer plastics. They measure between 1 and 100, with the higher number representing the harder material. As an example, tyre rubber is between 50 and 70 on the Shore A scale, dependant on the application. This link has a great chart explaining the Shore scale:http://www.quickparts.com/LearningCenter/ShoreScale.aspx
The reason it is so important to us is that we need to know how hard our finished mould or piece will be. If you are moulding an item or sculpt with a lot of deep undercuts, you need a bendy, flexible mould, so you couldn't use any silicone with a Shore A greater than say, 30. If you dont need to worry about undercuts and require a self supporting, rigid mould, then you would choose a silicon with a Shore A of greater than 30, and maybe even as much as 60 or so. If you are using silicone to make an item, be it a sculpt or a prosthetic appliance that will be glued to the skin, it is crucial that you know the hardness. If you are making a body part, then think- is it a flexible bendy part, or a stiff, bony part? Does your piece need to be soft and floppy, or stiff and self supporting? Choose accordingly.... Often the suggested applications will tell you what this product is best suited to. Our Proskin has an extremely low Shore A hardness, at 12, which is eminently suitable for the ideal purposes of skin-like products. M4503 is a fairly soft 25, so it is a fabulous moulding material for very detailed models with large or deep undercuts.
(*Note: SFX Prosthetics is a particularly specialised area and there are certain silicones that have been specially formulated with a third component that adds even more 'fleshiness' and 'stickiness' without affecting the cure.)
There are several other measurements that are relevant for industrial mouldmaking applications, but probably of less interest to most of us using silicones in the film industry. They include Tensile Stength, Elongation, Tear Strength, and in Tin Silicones, Linear Shrinkage and Expansion factors. We wont be going into those but information is readily available for those who are interested.
In the next part of what is turning out to be a slightly longer series than I had anticipated, we will look at using the silicones.
Summing Up- Important factors in your choice:
1. Colour- Do you need to see through your mould for careful removal of the item, or accurate placement of a prosthetic?
2. Pot-life and demould time- are you in a tearing hurry or can you afford to take time?
3. Compatibility- remember from Part 1, you can cast Platinum into Platinum, and Tin into Tin or Platinum, but you cant cast Platinum into Tin! What are you moulding, and what will your final piece be made from?
4. Viscosity- if you are pouring a matrix mould or a box mould over an intricate piece, you want runny. If you are brushing silicone over a large or vertical surface you want thick. Sometimes you need a combination of both.
5. Hardness- what does your silicone have to do? This will limit your choice to hard (High Shore A) or soft (Low Shore A) materials.
Using Your Silicone
So you are now fully equipped to choose exactly the right silicone product for your purpose, and you are champing at the bit to get started. So lets look at how to do that.
I'm not going to go into the entire multifaceted sculpting and mould-making process here, it would take me six months, and there are already a lot of fabulous resources out there.... what we are going to look at now is the actual silicone itself and what you need to do to end up with a usable product at the end.
There are several things to do before you even open the product.
FIRST, make sure your workroom, tools and materials are neither too cold, nor too hot This, I understand, can be tricky.... but especially in your first few attempts with silicone, it will make the process much smoother and increase your chances of success. (All Technical Data sheets list the estimated geltime and total curing time of your product, at an ideal working temp of around 24C (about 75F).)Wait a minute- chances? You mean this isnt a guaranteed, easy peasy, smooth as pie process? Weeeelllll.... technically, yes, it could be, as long as you follow the instructions perfectly and work in optimum conditions. But Im not going to lie to you- there are many things that can go amiss if you aren't careful, and sometimes, even if you are...
SECOND, assemble your tools and materials. You will need to make sure your materials and workspace are clean, and all components are compatible with the silicone of your choice- remember your list of inhibitors. You really need to have an accurate electric scale measuring by the gram for working with silicones, plus a pocket scale that measures by 0.1 grams, especially if you are making prosthetics and the likes that use only small amounts. Dont forget the calculator and a notebook to write things down- NEVER assume you will remember it all. Also, you will need to make sure you have CLEAN CONTAINERS. Never try and skimp on this... as my 16 yr old observed, recycling isnt a large part of Special Effects, and although we can re-use some things, it pays to be scrupulous when working with something as fussy and expensive as silicone. You can save a container you have used for the same silicone before and remove the old cured mix, but if there are uncured parts you are best to dispose of them and start again. Some cardboard cups contain wax that can inhibit some silicones. Clean paper cups, plastic containers or foodgrade plastic buckets are best.
THIRD, it goes without saying that you should ALWAYS test your materials before starting your project. It also goes without saying that most people simply don't bother....
Just to remind you why testing is a good idea, I have recently had a couple of people approach me with problems they have had with platinum silicone failing to cure properly, even when they had, in theory, done all the right things, and no causes were immediately obvious. Imagine if you ran a large workshop, and you were commissioned to create a large sculpture, lets say, a baby dinosaur, (around the size of a small pony). You can imagine that something that size is going to require a lot of material, maybe as much as a couple of hundred kilograms of silicone between the mould itself, and the skin of the finished piece. Oh, and it has to last, too, so it would be need to be Platinum rather than Tin silicone. Just for argument sake, we will use a base cost of around Au$70 per kilo of silicone. Lets imagine your total material cost for silicone in the mould and finished sculpt might then be as much as $14,000.... Would you just start right away, or would you do a test first? Of course you would! Yes, you have used that particular brand of Non Sulfur Plastilene for sculpting before, and that exact brand of silicone, and its never failed. Yes, you are an expert at fibreglassing, and you know better than to use fresh fibreglass moulds with silicone, and naturally you have a drill mixer and a vacuum degassing chamber. But even then- could you afford to take chances with $14,000 worth of materials?
True story- a certain large lab did indeed have a dinosaur to build, and -having done their usual thorough and comprehensive materials tests-, proceeded to make the case mould for their dinosaur. (A case or matrix mould is made by covering your sculpt with a layer of protective material like paper towel or plastic, then wet clay, then building your shell mould over the top. Once the fibreglass (or plaster) shell is set and cured, the pieces are separated, the wet clay and protection is removed, and the gap between the sculp and the case is filled with silicone through pouring holes, to produce a flexible inner mould capturing perfect detail and allowing a certain amount of undercuts.) After the allotted time for the cure had elapsed, the fibreglass outer shell was dismantled, and whoops- one particular section on the flank had completely failed to cure!!! It was surmised that an airborne contaminant must have drifted from another area of the workshop at some point and settled on an exposed area of the sculpt, where it later inhibited the cure of the finicky Platinum Silicone. As a result they had to discard the entire silicone inner of the mould, cut out that whole contaminated section of the sculpt, redo it and retexture it, and repour several thousand dollars of material. This story is not relayed to deter you, merely to inform.
Now before you give up and abandon silicones forever, I have a confession- I have been using silicone for years, and the only curing problem I have EVER had was trying to set Platinum silicone in a fresh fibreglass mould, resulting in a full head mask set perfectly against the plaster life-cast, and with a surface like unset jelly! I managed to salvage it by stippling the surface with a very fine layer of fresh silicone which set against the jelly and provided a usable piece. As it was a zombie, the loss of fine detail wasn't as much of an issue as it would be in a character makeup. A week later when I needed to cast the second mask, the fibreglass mould worked fine!
So, to sum up: If you make sure you have a clean workspace, at the right temperature, measure components accurately, and mix thoroughly, and your subject is non-inhibiting, then your product should behave exactly as it says on the packet!
Other Suff you Should Know:
ENCAPSULATION is a word you will hear a lot in relation to prosthetic silicone appliances. It comes from the Latin 'capsula', diminutive of capsa, box, and simply means to encase something in a sealed outer skin. In terms of silicone it i is only required when you are using a softening agent. In Platinum Silicones such as Platgel 10, commonly used for prosthetic appliances, it's usually Smiths Prosthetic Deadener, which is a specific product developed to add a 'fleshy' quality to the silicone. Smooth-On makes their own range of silicones or this purpose as well. (A general workaday alternative for non-prosthetic pieces where there is no skin contact is silicone oil). The reason you need an encapsulant is that the Deadener makes the silicone set very tacky- it never loses that gooiness it has in the gel stage even though it has set, and thus it will stick to everything and everything will stick to it! So for delicate facial prosthetics the pieces are encapsulated with a layer of an alcohol soluble plastic, called Super Baldiez, developed by Mouldlife. (This technique WILL NOT WORK with other kinds of liquid plastics or bald cap materials!). When these pieces are applied to the skin, the outer edge of the piece, which is a thin membrane of pure Super Baldiez, is then dissolved with 99% isopropyl alcohol and melts away onto the skin, leaving no visible edges on the prosthetic. Sheer beauty in a simple to make and apply form!
It is also possible to encapsulate pieces with a thin layer of platinum silicone with no Deadener added. This would be for a mask, or more robust pieces for repeated use (eg theatre or casualty simulation). Or when you want to make indiviual seperated body parts that have a natural fleshiness and softness.
Time to mix your silicone!!
1. MEASURE - How much silicone do I need?
Calculate the amount of silicone you will need to fill your mould. If you are a maths whizz you will already know all of this and probably accuse me of oversimplifying!! For the rest of us normal human beings, here's the easy way. DON'T CONFUSE WEIGHT WITH VOLUME!!!!!!! Silicone is sold by weight, so to calculate the amount of silicone you need, we need to know how much (VOLUME) our mould will hold, and then the equivalent weight of material (MASS) to fill the volume we have calculated. If its water thats pretty much 1:1, but Silicone has a higher Density than water so its weight is greater than its volume. *Mass is how heavy something is. Density is how heavy it is for its size, eg a kilo of lead is small and therefore very dense, while a kilo of feathers may weigh the same but it takes up a lot more space, so it is less dense....
Use the following formula: Volume = Mass/Density, and Mass = Volume x Density, The Technical Data sheet will give you the Specific Gravity, or Density, for your particular silicone. Density is TEMPERATURE SPECIFIC, so this only works really accurately if your silicone is at or around the ideal temp given on your sheet of about 23C. As a rough guide, many things get denser as they get colder due to shrinkage. Obviously this isn't an issue with small quantities, but in a large mould it can result in an expensive mistake.
For a small, simple Box Mould, glue your item in place on the base, (or if it is a Two Part Box Mould, embed it halfway into clay in the bottom half of the box,) fill it with water and then measure that water to give you the volume of the mould. Multiply the Volume by the Density of your Silicone. TOP TIP: if it is a 1:1 mix, you can simply halve the required volume and mark the resulting volume on a container for each component, eg 1 litre of water gives you a half litre of each component, fill the containers to the 500ml mark and there you have it.
If you have a flat Plate Mould, for which we often use cardboard strip or wooden strips to build the sides, the water trick won't work... but you can measure the depth, and approximate the square centimetres by measuring the sides. For example, a mould of a 30cm square board that has to cover several small flat sculpts of scars, 1 cm high at the deepest point, would be calculated thus: The dimensions of a square 30cm x 30cm = an area of 900 square centimetres. We know our mould has to be at least 5mm thick above the highest point of the sculpt, so we calculate the required depth at 1.5cm. 900 x 1.5 = 1350, or 1.35 litres.
To clarify, the AREA, (900 centimetres squared) multiplied by the DEPTH (1.5cm) gives us a VOLUME, or CUBIC CENTIMETRE measurement of 1350 cm3. A litre in volume is 1000 millilitres or 1000 cubic centimetres or 1000 m3, therefore our required volume is 1.35 litres. Multiply the SG of your silicone by the volume, lets say you are using one with a Relative Density, or Specific Gravity, of 1.16. You would have a Volume of 1,350 cm3 (1.35 litres) x Density of 1.16, giving a Mass of 1.56kg. You need to use 1.56 kg of silicone to fill that mould. TOP TIP: If you have an old cured piece of a similar silicone of the right thickness sitting around, you can always have a rough guess how many of those pieces would cover the area of your mould, weigh the piece, multiply the number by the weight and that will give you a good guide.
If you have a Matrix or Case Mould, take all the wet clay you used to cover the sculpt and build your shell over, stuff it into a bucket of known volume and then use that to approximate the volume. Alternatively, measure the weight of a known volume of clay (say 1 litre), work out the weight ratio between the clay and your silicone, and use that to calculate the equivalent quantity of silicone.
If you are making a Brush-up Mould it's a little trickier and will be a guesstimate at best, but remember you can always add more layers and build up your mould as you go. You should also use an unthickened surface layer first to capture the fine detail in any case.#]
"But Im not making a mould, I'm taking a Lifecast... " Each of the special Skinsafe Silicones that are designed for bodycasting will have information on the manufacturers website listing the approximate quantity needed for various bodyparts. Be especially careful with these silicones as temperature has a HUGE effect on their setting times and that can really mess you around. If you mix up too much and it sets before you get it on that's an expensive waste. Best to do a thin layer first then mix another batch and add a second layer.
Once you know the Volume and have worked out the Weight (Mass) you need, weigh out your components in the correct ratio. If your silicone is a 1:1 ratio, then halve the total volume and measure each half separately in a clean container. If your silicone is a ratio of, say, 1 part Catalyst :10 parts Silicone or higher, calculate the weight of each part by adding the TOTAL PARTS of silicone (1:10 = 11 parts total, 1:100 = 101 parts etc) and then dividing the required Mass by the number of parts. E.g. For a mould needing 2.4 kilograms of silicon, if you are using 1:1 silicone, that gives 1.2kg of Part A and 1.2kg of Part B. For a silicone with a ratio of 1:100 (10gms for every 1000gms or 1ogms per kg) you will need 2400gms/101 = 23.76, so that means 23.76 gms of Catalyst to 2.376gms of Silicone.
Additives
Pigments-
Many mouldmaking silicones have a clear or white part and a coloured part, which helps in mixing. When you are using a translucent silicone you may want to add pigment for the same reason, and if you are making a final piece, you will often want to colour it. If you are adding pigments follow the recommended instruction as to which component to add it to, and mix thoroughly before combining your components. Be sure to follow recommended ratios to avoid inhibition.
Retarders/Accelerators/Thixotropics - Accurate measurement is crucial. Thorough mixing is also crucial. FOLLOW INSTRUCTIONS CAREFULLY!!
2. MIX - How do I mix my silicone?
One particular manufacturer has the charming recommendation on its product information that if you intend to mix your silicone by hand, they recommend three or more years of experience as a commercial cook first!! They arent kidding..... although Tin Silicone is pretty forgiving, and a few unmixed streaks will probably cure regardless, Platinum is much more finicky and must be thoroughly combined. The recommended methods for mixing are similar for both kinds, but the major determining factors of method are your POT LIFE and VISCOSITY.
An important thing to note when mixing silicone is that if you mix thoroughly and vigorously like you are supposed to, you will get loads of air bubbles in the material. The thicker or more Viscous your material, the easier it is to make bubbles!! This is not good, as those bubbles can stick to the surface of your sculpt or model, and also weaken the structure of the mould. If we get bubbles in it, they need to be removed either before or during the pour (see 3. POUR). Platinum silicones with a very short potlife must be mixed very carefully because the silicone will likely gel before the air can be removed. People who do a lot of large silicone pours will do well to invest in a Vacuum Degassing Chamber, which creates a negative air pressure around your mix and 'sucks' the air out of the silicone, but if you are reading this, I am going to assume that either you don't have access to one, or if you do you wouldn't know how to use it anyway, so we will look at other options here.
MIXING BY DRILL
If you have to make a large mould or item, you will need to choose a silicone with a LONG POTLIFE. This is essential because it will allow you to mix thoroughly and still have time to get the air out. I recommend a drill mixing attachment- there are a couple of different kinds you can get at the hardware store that attach to your electric drill and are designed for paint stirring, they rotate and work kind of like an egg beater. You also want one with a fairly low VISCOSITY because it is easier to pour. Once you have thoroughly stirred the two halves of your mix, scrape the sides down and make sure you havent left any unmixed material in the corners of the base of your container, then mix it again!! Now you can let it sit for a little while, no longer than about a quarter of the time of your potlife (not including mixing time) to allow bubbles to rise towards the surface.
MIXING BY HAND
If you are making a smaller mould you can use a shorter POTLIFE, and you can use a hand method like a paint stirring stick, or with very small amounts even the disposable flat wooden spatulas.... Using a figure eight motion combine the components and take care not to 'beat' but to 'fold', so as not to incorporate too much air. Scrape the sides and the base of the container thoroughly every few stirs. Always mix as much as you think you need, then do it again, just to be on the safe side.
POUR - How do I pour my mould?
You have your model, sculpt or item, and you have chosen your mould style.
Important point to remember- silicon is dense and heavy. It will follow gravity. It has a particularly alarming tendency to find any pinprick gap in your mould wall or casing and ooze out. It also finds the lowest point in any situation and pools there. Which means that if you do not take steps to anchor your object, cast or item very, very, thoroughly to the base of your board, (superglue works well).... you may find that instead of the silicone covering your object, even a heavy item will instead soon be floating on top of the silicone!
To pour a Box Mould or Plate Mould, this is the best way to remove air bubbles and cover evenly. Place mould on a level floor. Stand on a chair. Hold mixing container carefully as high as you can without spilling it, and VERY SLOWLY pour a very thin stream of silicone so it pools in a corner of the mould, preferably not directly onto your sculpt. This allows the silicone to rise up over the sides of the piece, pushing any air bubbles away from it and finding its own level. As the silicone stretches, the encapsulated airbubbles will stretch and burst so that the silicone hitting your mould has very little air in it, and hopefully those bubbles will find their way to the surface easily. TOP TIP: Be aware that if you have significant undercuts, you may need to do at least part of the pour with the mould at an angle to prevent the air bubbles being trapped under overhangs. Once you have finished the pour, transfer your mould to a safe (level) place like a tabletop, and bang carefully underneath the table to encourage air to rise. If you are using a transparent or translucent silicone, and you can see airbubbles on the surface of the sculpt, you can pop them with a popstick or a gloved finger. Then blow gently on the surface from time to time until it has gelled, to pop any emerging bubbles. You can use a straw to do this for directed effort....
To pour a Matrix or Case Mould, you will have left holes in the hard shell mould for filling, and also placed small holes in undercuts for air to be squeezed out. Normally you would use either a funnel and do the same trick as the flat mould, that is, pouring from a height, slowly, or if you are using a thicker silicone, it is possible to make a syringe type arrangement, either by using a clean, unused Foam Latex Injection gun, or improvising with a large Drain Plunger. (As long as you can get pressure, and there is nothing in the plunger like a latex rubber seal that could inhibit the silicone, it will work). As the silicone starts to reach the airholes and ooze out, plug each one with a screw and keep pouring till you reach the top of the mould.
Brush-up Moulds, as the name suggest, use a thicker silicone and you simply brush on layers until you have an adequate thickness over your surface. Usually you would use a thin silicone first to capture detail, and just keep scooping it up and pouring it back over the top as it runs down the sides, until it begins to gel. Then you can apply a thicker layer, either using a special silicone designed for brushing or by adding a Thixotrpic Agent appropriate for your silicone.
WARNING: not all silicones can be effectively thickened, and some only work with their own specially composed additives. There are different Thixotropic Agents for Platinum and Tin silicones. Dont mix them up. Some silicones thicken a lot, others hardly at all. TEST TEST TEST!!!
PROBLEMS:
Oh-oh, I Don't Have Enough Silicone and the Store is Closed, Can I Mix Two Different Kinds? - You cannot mix different types of uncured silicone. Each is specially formulated to give a specific result and wont work correctly if you mess with that. You can however add another layer on top of the first once it has passed the gel stage, and the silicone will bond quite happily, as long as you remember that Tin on Platinum = :) and Platinum on Tin = :(
Ok, that may not have been entirely true... You CAN, in some circumstances, mix silicones, but only if they are of the same kind (Platinum - addition cured, or Tin - condensation cured,) and the same basic ratio. It is probably not going to work if you attempt to mix one that has a 1:1 ratio with one that is 100:1.... ! In any case it is best avoided until and unless you have a fair bit of experience and a good understanding of the materials behavioural characteristics.
Silicone Hasnt Set
There are different types of inhibitions. If the contamination you have experienced is classified as 'minor', it will be 'tacky' or 'wet' looking, and only on the surface. If it is really like unset jelly but only on the contaminated side, that is 'serious inhibition', and 'very serious' would be if it is still semi-liquid or not setting anywhere.
Sometimes it means there is something in the clay, or the object you are moulding, but if you had done tests you wouldn't have had this issue. ;)
If it is something added in the course of sculpting the clay thats trickier. Interestingly in one products info page I found this"Residual solvents or monomers that may inhibit cure:• Chlorinated hydrocarbons that contain amine stabilizers• Alcohols– Ethanol, methanol• Esters– Ethyl acetate, vinyl acetate•Compounds with unsaturated bonds"
Those are known as ' temporary inhibitors', which means once they evaporate out they do not affect the cure, as opposed to permanent inhibitors which cannot be gotten rid of. Sometimes if you havent let the solvents evaporate completely from your sculpt this may affect the cure, but if you leave the mould for a few days it can sometimes still set properly, eventually, as the solvents disappear.....
"Residual solvents that do not inhibit cure include Nonchlorinated aromatic and aliphatic solvents– Toluene, xylene– Hexane, mineral spirits".
Stuff like Lighter fluid and Naptha therefore shouldn't cause problems, but isopropyl alcohol can.
I also recommend covering your sculpt between working sessions, to avoid the chances of any airborne contaminant landing on it. (Remember the dinosaur..)
If the room temperature is cool, that can interfere. Low temperatures in itself wont stop curing, it just slows it down. A rule of thumb I remember from somewhere was that every ten F below 73 doubles cure time. Which means every 5-6C below 23C will double cure time, however you can blast it with a dryer or heater once it has gelled to stop that, or even rig up a 'hotbox' under a coffee table or large box to give it a warm environment.
Years ago when silicone first came into FX use there weren't any room temperature catalysts and they had to use heat to set it. Even when they invented the RTV process the guys in workshops couldnt get platinum silicone to kick at all in their workshops because of all the latex they used and the foam latex they made- the air was fullI of ammonia and sulfur...... (In factories and large workshops these days they use industrial filtering equipment to clean the air of any gaseous contaminants to stop problems)How Do I Fix It? - If you didn't do a test, you went ahead and poured your mould, and a Platinum Silicone doesn't set against your sculpt the first time, you have a couple of choices. Uncured silicone is notoriously difficult to remove. You may be able to remove the majority by using an absorbent material, beginning with paper towel and ending with talcum or fullers earth. Then once you have removed all you can physically, you will need to resort to cleaning agents, the gentlest of which is 99%isopropyl alcohol, and the stronger of which is Naptha or Lighter Fluid. All require good ventilation and breathing protection. All solvents will damage the surface of your model if it is a sculpture made in plastilene. IF you can adequately remove the uncured product from the model, you may be able to try again. Retexture your piece. Seal the sculpt THOROUGHLY by using a couple of fine coats of clear lacquer or similar, which will inevitably result in some loss of detail. This MAY solve the problem, but dont go and pour a whole new mould before testing a small patch. If you can't bear the thought of resculpting from scratch, you could try using a Tin silicone for the mould casing, and then make a plaster positive, which you can then remould in Platinum silicone. Still- test first!! A long process, but take note- it is also the only way to work if the item you are moulding is itself made of something incompatible with Platinum silicone. Your other option is to start from scratch and TEST TEST TEST!!!
Here is a second article that I found by Stuart Bray, he details the uses of the different silicones for various moulds. It also notes the desired environments for the silicone along with some issues that can occur in the process and how they can be prevented and rectified.