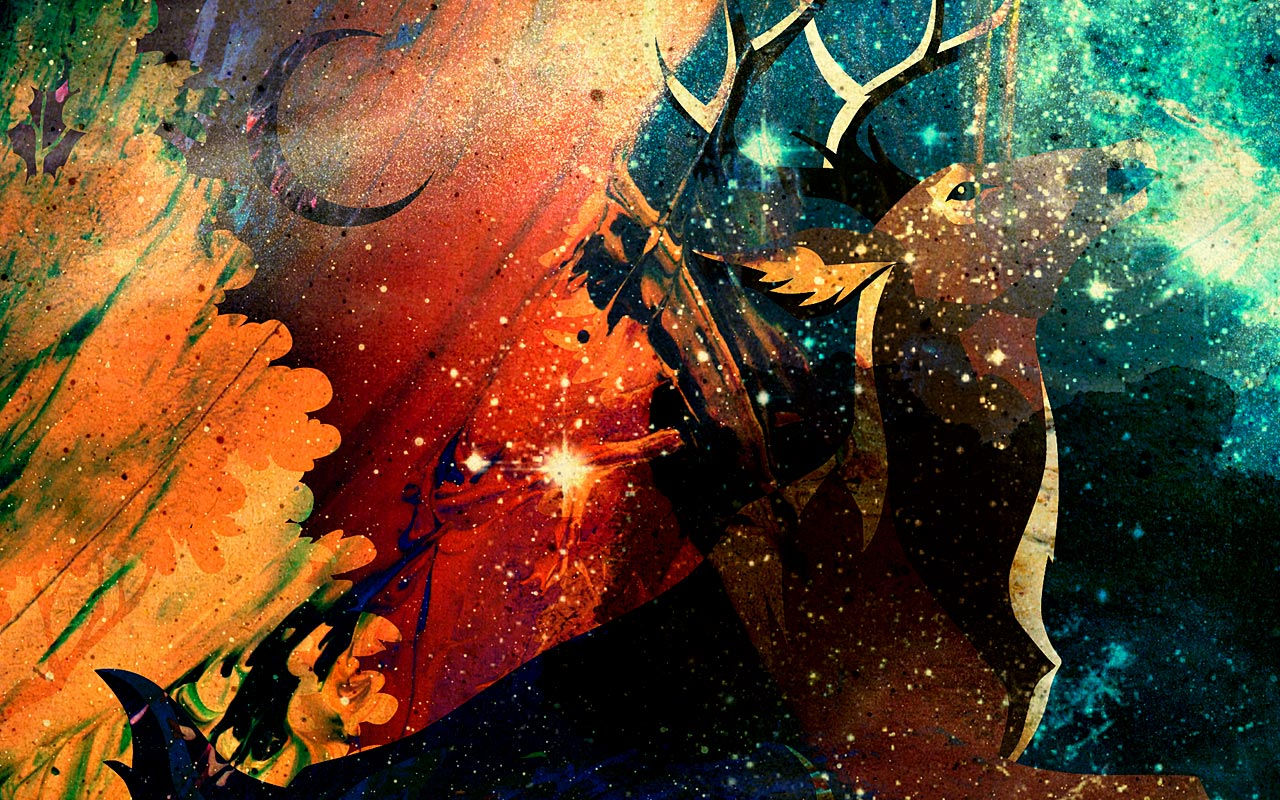
KW
Horn
For the design the horn is the focal piece of the makeup therefore it is important that I make it as realistic as possible. I have previous experinence in making small spines for the last project, however this is a whole new level. I have to create a very large horn and make it as lightweight as possible in order for the model to wear it for long periods of time. It will also need to be removable as the actor will not fit into the car with the horn on the top of the head to get to the location. To do this I have thought of a way in which the horn may attach to a vacume formed plate that will be placed under the prosthetic with a bolt attached. The horn will then have the corresponding bolt that will allow it to be removed easily.
To begin the process of creating the horn I took the lifecast of my model, I then created the casts in fibreglass. Once I had these I was able to work out how long the horn needed to be in order to reach over the head and pierce into the back of the design. After gathering the indormation for the length I began sculpting the horn with a foam inner in order to save time on structuring and building up clay. However the I didnt take into account that the foam needed to be smaller that the desired size, to allow for the clay and textuing, which made it difficult to sculpt without touhing the foam. Once I had completed the horn I coated the clay in a fine layer of silicone to pick up the detail, I then proceeded to build up the layers to get a thick mould. Once moulded I removed from the fibreglass head and created a fibreglass jacket around the piece so that I could run the piece in fast cast and rigid foam. To do this I placed the silicone mould inside the fibreglass and poured fast cast around to coat the outer layers. The next step was to mix rigid foam to fill the inside, this made it as lightweight as possible. The photographs below show the process of creating this horn. Once I had the final horn I was able to use it when sculting the caul piece to ensure that the final prosthetic fit snugley around the piece making a cohesive piece.
![]() Hot Wire SculptorThis is the original foam that I began with, it was already partially used, therefore it was not quite big enough for the horn that I wanted to create. However I made do with it the best that I could. The wire cutter was really effective, activated by a foot pedal it cut straight through the foam leaving a very smooth finish. | ![]() Foam HornThis image shows the foam mid cutting, it cuts straight through the foam. I tried to create the basic shape of the horn in the first cut, however I had to cut multiple pieces as seen in the later photographs. | ![]() Foam HornHere is the basic shape of the horn that I created without the extension segment that I had to create to bring it back round into the back of the head. The horn is still in the rougher stage here, and has more shaping required. I really liked this process as it worked really effectively, saving on material in terms of clay usage and allows for less time spent making a wire structure. |
---|---|---|
![]() Foam HornThis is the final form of the foam base that I created. due to the amount of foam that was available to me I was not able to create the entire horn base in one piece so I had to attach the extra tip on the horn using some small rods that I placed in both halves. | ![]() Final ScukptUnfortunately I lost the images from the sculpt before mould the horn, this is a photograph of it after the moulding process, there is a little distortion on this side however it is mostly as it was before. | ![]() Final SculptThis side of the horn sculpt received a lot more damage from removal of the silicone mould. The general shaping an indentations with grooves are still visible showing the style of the horn that I created. The final horn came out a little distorted due to the pressing of the fibreglass, so the final horn is not quite as I sculpted, however it is very similar. |
![]() Drill BitI used this drill bit to create a small indentation in the wood board that I was using as a base. I then screwed a screw through the wooden board in order for the horn to be held upright in order to hold the horn during the moulding process. | ![]() Silicone Mould of HornHere is the horn attached to the wooden board with the screws and the first layer of silicone 3481 to pick up the detail. As I had done this layer with the horn lying down it meant that I had to cut the excess off the and there were slight gaps in the silicone which meant that I needed to be careful when applying the next layers to not get air bubbles. | ![]() 1st Mould WallI built a wall out of wet clay to support the first half of the fibreglass mould. I used small circular keys and larger more block like keys in order that the two halves fit together really well. However due to unseen circumstances I was unable to mould the horn until the end of the day and the lay had dried up making it impossible to use. I also needed to apply more silicone as it was too thin for multiple moulds in case I needed another horn. |
![]() 2nd Mould WallAfter applying more silicone to the horn I rebuilt the wall in a similar style to the first. This also had small circular keys. This wall worked well. However I had very little time to mould the horn so there was no gel coat and the result was quite rough, however because it was simply to hold the silicone mould it didn't matter too much, other than aesthetically. | ![]() Fibreglassed hornThis was the first half of the fibreglass wall that I created, This worked alright and wasn't an issue, I found it hard to not get air bubbles around the keys and the corners of the horns however it worked well enough. | ![]() Fibreglass HornHere you can see the two halves together, as I was fibreglassing the horn until the very last moment on the friday, it meant that I did not have time to vibrosaw the edges neatly. This was due to the necessity to run the horn by the next week. |
![]() Fibreglass HornThe second half that I created was the one on the left, this is due to the clay not being present. I was only able to use fibreglass matting as the veil had run out at this stage. If I had more time I would have liked to have cut the excess off the fibreglass to try and make the mould a bit neater. | ![]() Fibreglass HornThis is the first half of the fibreglass mould after removing the wet clay wall. I did not have time to properly clean up the inside before having to make the second half of the mould which is where I began to get unhappy with the result. If I had the time I would have spent much longer making sure that the mould was neat and perfect. | ![]() Fibreglass HornHere is the opening to the silicone mould of the horn with the two halves of the fibreglass bolted together. It was into this entrance that I needed to first pour the fast cast resin in order to make the outer layer strong. I swelled the resin around to make sure it covered the whole area then filled the inside with rigid foam to make the horn lightweight and solid. |
![]() Expanding Rigid FoamThese photos show the before and after of the rigid foam. This is after initially mixing the parts A + B of the foam it turns a creamy colour after a moment or so the material changes colour. | ![]() Expanding Rigid FoamThis is the foam after the creamy colour has dissipated, it begins to turn a brown colour and show lots of bubbles in the mixture, once it reaches this stage it should be poured into the mould to fill the centre. | ![]() Horn Pre ColouringThis is a photograph of the horn after removal from the silicone mould. The fast cast resin turns white when it is set, creating the white colour on the outside of the horn. This colour works well as I was trying to create the effect of bone of which the base colour is white. |
![]() Final HornHere I had begun to colour the horn using a slight cream, brown and pink tone. I used elephant tusks as reference for colouration as I felt that these were the most suitable design that would work with my character. |

This is the elephant tusk picture that I used as refernce for the horn that I created for my character I tried to imitate the styling and also a little of the colour, however I changed it slightly as the creature was an original design.
Creating the Cap for the Horn
For this horn to be attached to the models head it required a base that would support the weight and keep it in place. To do this I thought that I would create a vacuum formed cap of my models head, into which I ould cut a hole and insert a screw or bolt. However my model has a very large head and the fibreglass core would not fit underneath the plastic in the vacuum form machine. This meant that I had to create a fibreglass core I released the fibreglass core with lots of wax so that the fibreglass does not stick. I then applied a layer of matting with veil, however when I removed this it was very flexible and weak, therefore I needed to apply more matting to support the shell. I then applied two more layers and veil to make sure that it was thick enough. Once this was set I took it off the core and vibrosawed the edges off. I then made sure that the back edge of the cap did not restrict the movement of my model around the back of the neck by cutting it to size and trying it on him. Once cut to size I sanded the edges of the fibreglass and then lined the inside with chamois leather in order that the model have a comfortable cap on his head. I unfortunately lost the images of the process, however I will hand in the final piece in order for my work to be seen.
Elephant Tusk (n.d.) [Online Image] Available From: http://pixshark.com/elephant-tusk.htm Date Accessed: 27/04/2015