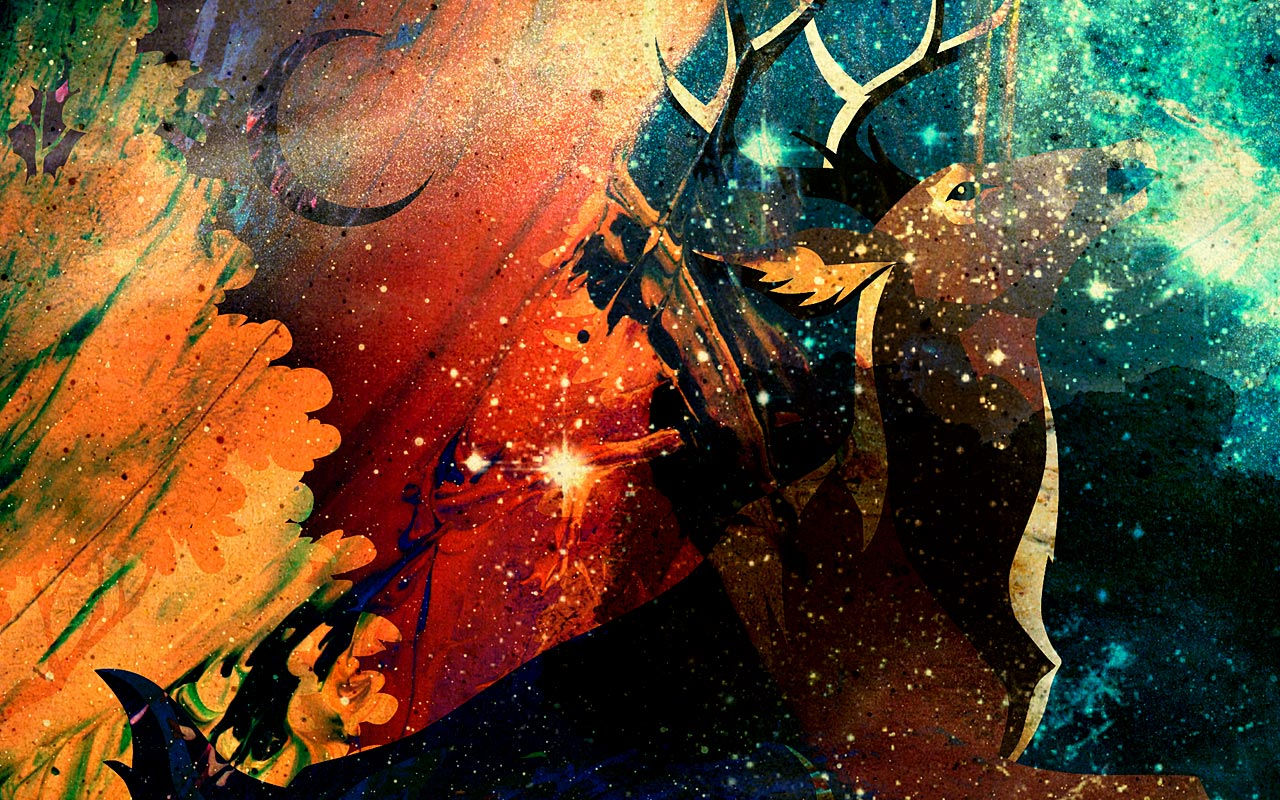
KW
Lifecasting
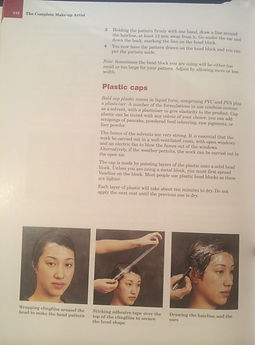


Although I have made bald caps before I thought it necessary to look over the notes and methodology again in order that I make sure my cap is as effective as possible. Therefore I looked through the Penny Delemar Book which showed the fundamentals of the technique. After re-reading these notes I have decided that it would be best to create a latex bald cap for the lifecasting process. This will be due to the fact that I do not know my model's head size at the time of casting and the latex is more likely to stretch whereas a cap plastic bald cap may rip. Trying to judge my model's head size from a phtotograph is not accurate, however it will give me a rough guide as to the size to create the cap. Delamar's book shows the technique to create the bald cap, reminding me of some small segments that I need to include in the process in order to have an effective cap. The cap will not have to be perfect, but good enough to withstand the stretch and keep the model's hair wrapped during the lifecasting process.
I created the cap using latex as I knew that this has more elasticity, I was happy with the result, however there were some slight bumps in the cap from small segments of dried latex sticking to the cap. I therefore decided to turn the cap inside out in order that the lifecast came out smoothly and made the process of cleaning up the fibreglass much easier.
Delamar.P. (1994) The Complete Makeup ArtistL Working in film, Fashion, Television and Theatre. 2nd Edn. London: Cengage Learning Vocational pg 242-244
Below are the photographs of the process of creating the full lifecast on my model, I had some helpers in order that the process went smoothly and the model felt secure. I got all of the equipment and materials ready before the application of the cast so that the time spent in the cast was as small as possible, trying to reduce any discomfort for the model as possible. Taking note of the research that I had previously conucted on the Full Head Cast page I approached this lifecast utilizing those techniques. I found them to be very helpful and allowed me to create a successful and effective lifecast.
![]() Applying the Bald Cap and BondoThe first step in the process of creating a lifecast is to cover the head with a bald cap. Most would draw the hairline with a permanent marker that would then transfer onto the material that the face is being casted in. At the time of casting I did not know if I needed the ears for the sculpt so I left them free. | ![]() Applying the Bald Cap and BondoHere I used a very small injection tube to draw the hairline onto the bald cap. I then allowed this to set as much as possible before lifecasting. As I did not have the models head measurements the bald cap did not fit perfectly, however it did the job. I cut the ears out in order that I could lifecast them in case I needed it at a later date. | ![]() Applying Plaster to the Back of HeadThe first step in the lifecast is to apply plaster to the back of the head. I did so with plaster bandages, with long smooth strips along the back to try to create the smoothest possible texture on the inside. I made sure to reinforce the plaster along the centre and around the edges as these would receive the most damage and need to be the strongest areas. |
---|---|---|
![]() Applying Plaster to the Back of HeadI think the lifecast was very successful, however the only thing that I would change is he amount of plaster I applied on the top of the head and also how far back the plaster went. On another cast I would bring the dividing line further forward so that the two halves were more evenly divided. | ![]() Applying Silicone to FaceThis photograph shows the first layer of silicone being applied. I started with a very thin layer to pick up all of the detail of the face. I then went on to cover this first layer with another two to ensure that the silicone was thick enough to not rip when lifecasting. I found the silicone very effective to use to create the lifecast as it applied very easily. | ![]() Applying Silicone to FaceThis shows the silicone after the layers has been applied. I found it a very effective material to use as it applied well with wooden spatulas. This allowed me to create a relatively smooth outer surface. |
![]() Applying Silicone to FaceI was very happy with the result, the only problem was that the silicone had not been mixed properly and did not fully cure around the ear area. This meant that when I pulled it apart the ears did not come out of the mould effectively and were not successful and did not come out in the fibrelass. There was also one area under the jaw that was very thin with silicone, it held together, however if I were to try to create another lifecast with it, I would have to be very careful to not rip the area | ![]() Applying Silicone to FaceHere you can see that the silicone successfully covered the face. The eyes were a main focus during application and had a good amount to ensure that the cast did not rip. The small area that was very thin taught me to be careful to ensure that the silicone is evenly applied all over the face as this could be a big issue if I had needed multiple cores. | ![]() Applying Silicone to FacePulling the two halves apart was quite challenging, as I had to try and get the face half around the ear, which is a natural undercut. The back of the cast came off first allowing me to see where the silicone laid around the ear and to try ease it out slowly. Overall it was a very successful lifecast allowing me to produce a good fibreglass core. |
Unfortunately I can no longer acccess the photographs displaying the front of the face in the plaster bandage. I helped out for the experience in order that I have a better understanding of the application process and I am able to achieve a more successful and faster application. I found that upon this second application I was much faster and the result worked very well. The lifecast that I applied used silicone whereas the second lifecast was alginate and therefore had a slightly different application however the results were very similar.
After the process of creating the lifecast in silicone the next step is to create the fibreglass cast onto which I can begin sculpting. This will be explored on the following page with research alongside in order to create the most professional result.